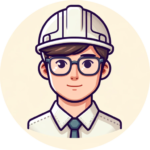
プラントで必要となる機器、特にタンクや配管は溶接が多用されている。安全に使用するためにも欠陥を防ぐことが重要だよ
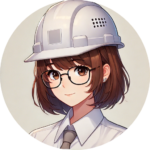
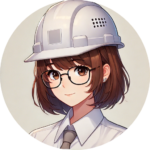
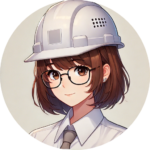
特に気をつけるべきところはどういうところですか?
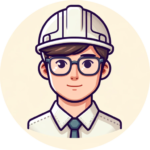
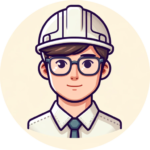
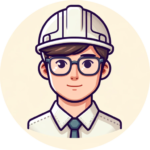
正直いうと全部だね。安全性に関わるから。特に高圧ガスや半導体などの毒性ガスを使用するところや、食品などの少しの欠陥が大きな問題になるところは絶対に避ける必要がある。
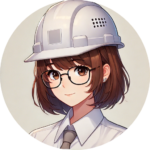
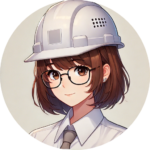
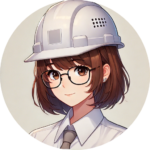
どういう欠陥が存在するかを理解して設計段階で対応していくことが必要ですね!
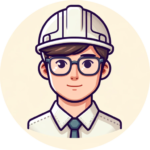
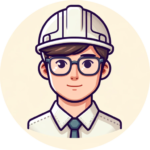
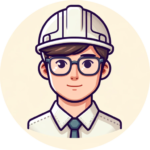
その通り!基礎的なことでも理解しておけば設計段階で十分対応可能だよ!
溶接は、金属同士を接合するための重要な技術です。プラント機器や機械製作の際にも、必ずと言っていいほど溶接で加工する部分が発生します。
溶接工程で発生する欠陥は、製品の品質や安全性に大きな影響を与えまず。特に高圧ガスなどを扱うプラント機器では、その欠陥から大事故につながる可能性があります。また、機械においても溶接欠陥部分を起因とする割れ、疲労破壊などで作業者に危険が及ぶ可能性があります。
これらの欠陥を予防し、適切に対処することがプラント機器や機械の安全性確保のために不可欠です。また、溶接欠陥は補修が難しい場合もあるので、事前に対策をすることは製作時間の短縮にもつながります。
本記事では、溶接欠陥の主な種類やその原因、防止策について詳しく解説し、プラント設計や機械設計、製造業や建設業に携わる技術者に向けた実践的な知識を提供します。
溶接欠陥の分類
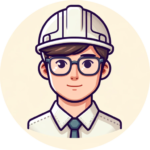
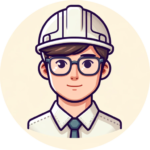
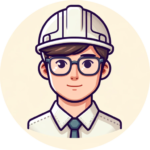
基本的な欠陥は外部にできるか、内部にできるかのどっちだね
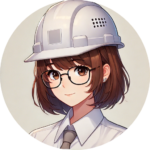
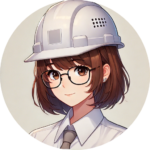
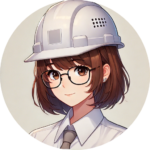
外部欠陥は発見しやすいけど内部欠陥は発見しにくそうですね
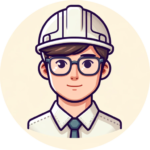
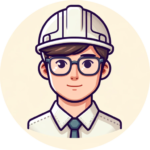
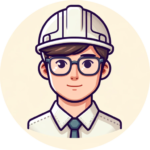
そういうことなので、いかに非破壊検査で欠陥がないかを見つけることが重要。
溶接欠陥は、大きく分けて「寸法・外観的な欠陥」と「内部に存在する欠陥」の2つに分類されます。それぞれの欠陥は、溶接部の見た目や構造的な強度に関わるもので、適切な検査方法を用いて確認する必要があります。
寸法・外観的な欠陥
寸法・外観的な欠陥は、溶接部の形状や外見に関する問題です。以下は主な外部欠陥の例です。
- 目違い: 溶接部が母材との間でズレている状態。見た目に不均一さがあるとともに、応力が集中しやすい部分が発生するため、構造強度が低下します。
- アンダカット: 母材に深い溝ができる欠陥で、過度な溶接熱や不適切な溶接速度が原因となります。
- オーバーラップ: 溶接金属が母材の上に乗り過ぎることで、融合不良が起こりやすくなります。
これらの欠陥は、目視や外観検査で容易に確認することができるため、製造過程での初期段階で発見されることが望ましいです。
内部に存在する欠陥
内部に存在する欠陥は、外観では確認できないため、X線検査や超音波検査などの非破壊検査(NDT)によって検出されます。代表的な内部欠陥には、以下のものがあります。
- 割れ: 溶接金属や熱影響部に亀裂が発生する現象で、構造上最も深刻な欠陥の一つです。割れは低温や高温の環境に応じて異なる原因で発生します。
- 気孔: 溶接中にガスが閉じ込められてできる小さな空洞。気孔は材料強度を低下させ、応力集中が起こりやすくなります。
- スラグ巻込み: 溶接ビード内にスラグ(不純物)が取り込まれる現象で、接合部の強度に大きな影響を及ぼします。
内部欠陥は構造の強度に直接的な影響を及ぼし、検査や管理が難しいため、溶接プロセス全体の精密な管理が求められます。
各種割れの種類とその対策
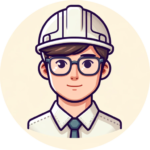
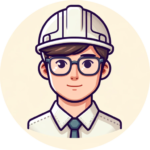
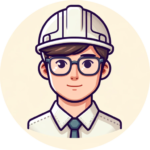
ここからはいろいろな溶接血管とその対策法を説明していくよ
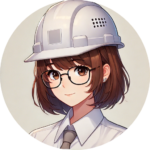
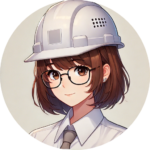
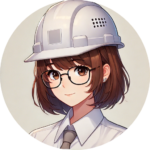
すごいいっぱい!全部覚えるのは大変そう!
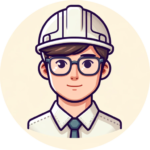
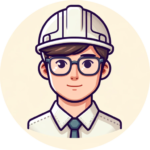
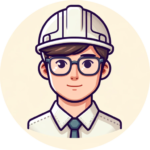
そうだね、でも設計にも必要だからしっかり覚えておこう
溶接部に多く発生する欠陥が割れです。割れは多くの種類がありそれぞれ原因と対策が異なります。
ビード割れ
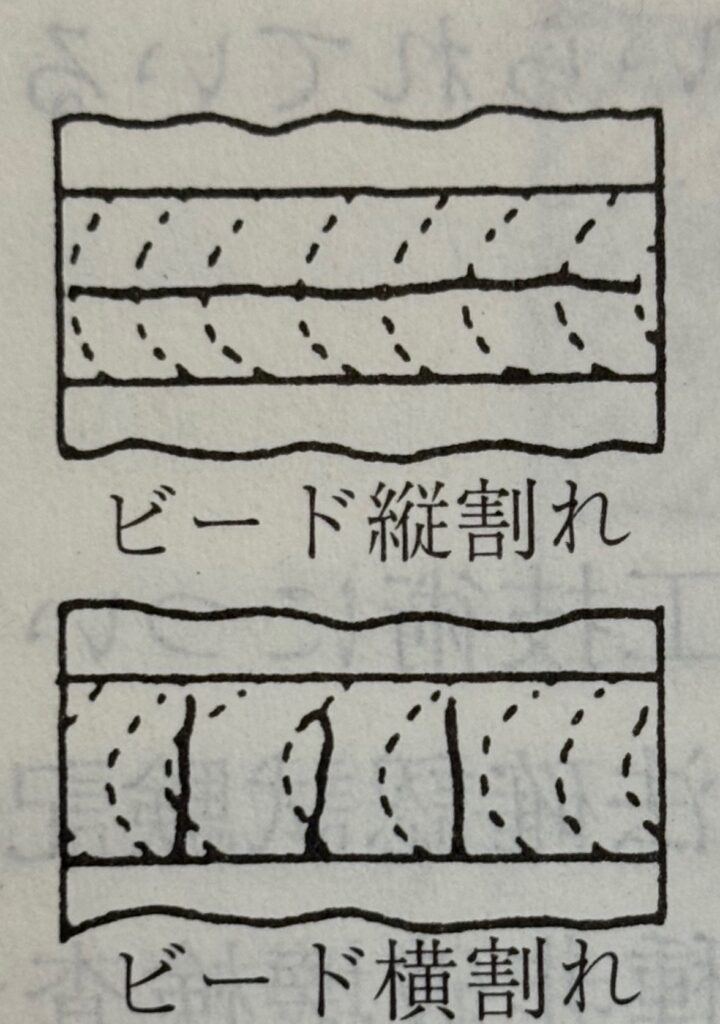
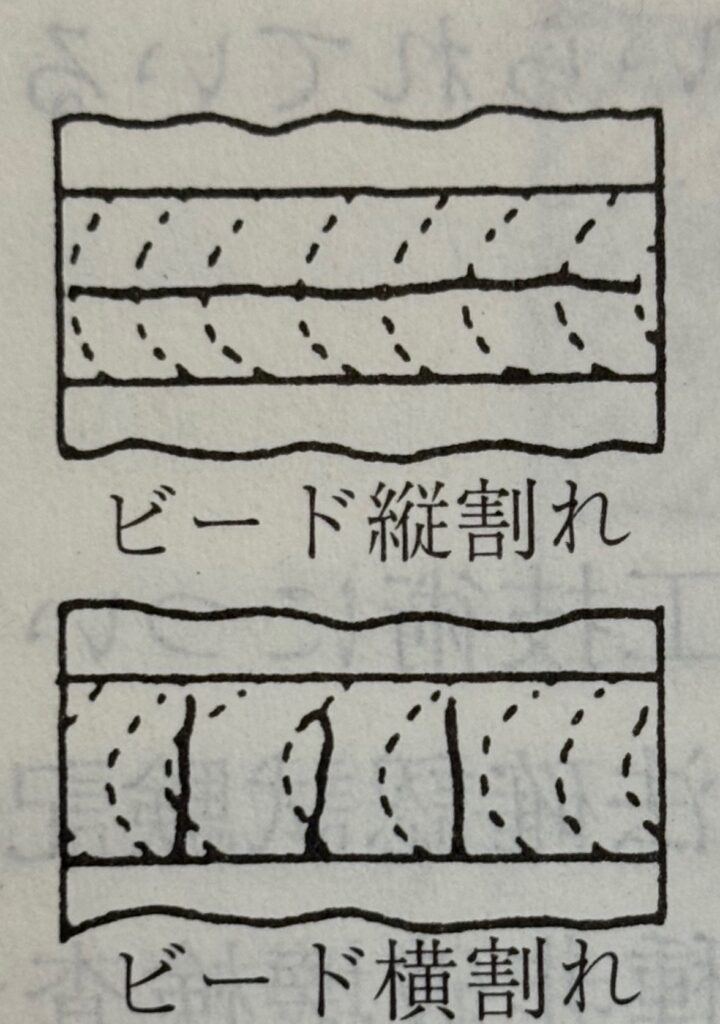
溶接ビードの途中または終端部分に発生する割れです。表面に現れることが多いです。原因としては 溶接時の熱応力や冷却速度の不均一、溶接金属の収縮などが原因となります。特に、溶接中に急激に冷却されたり、熱が偏る場合に発生しやすいです。
- 適切な溶接電流や速度の設定
- 溶接後の適切な予熱や後熱処理
- 溶接の順序や方法の最適化
- 冷却速度を制御して均一な熱分布を保つ
クレーター割れ
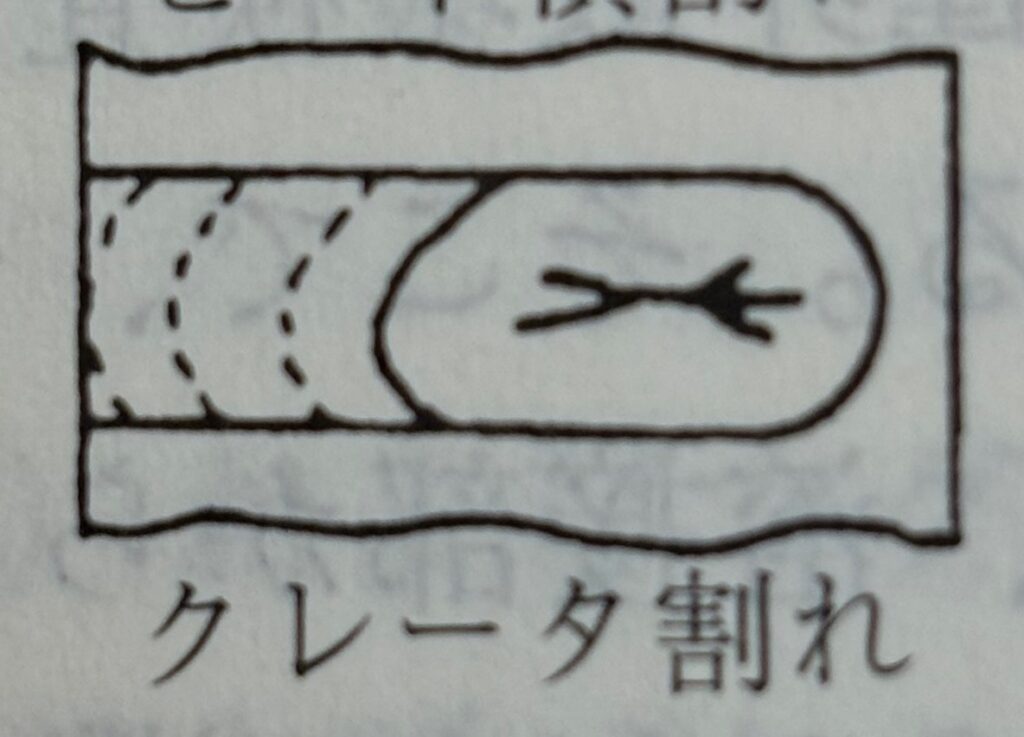
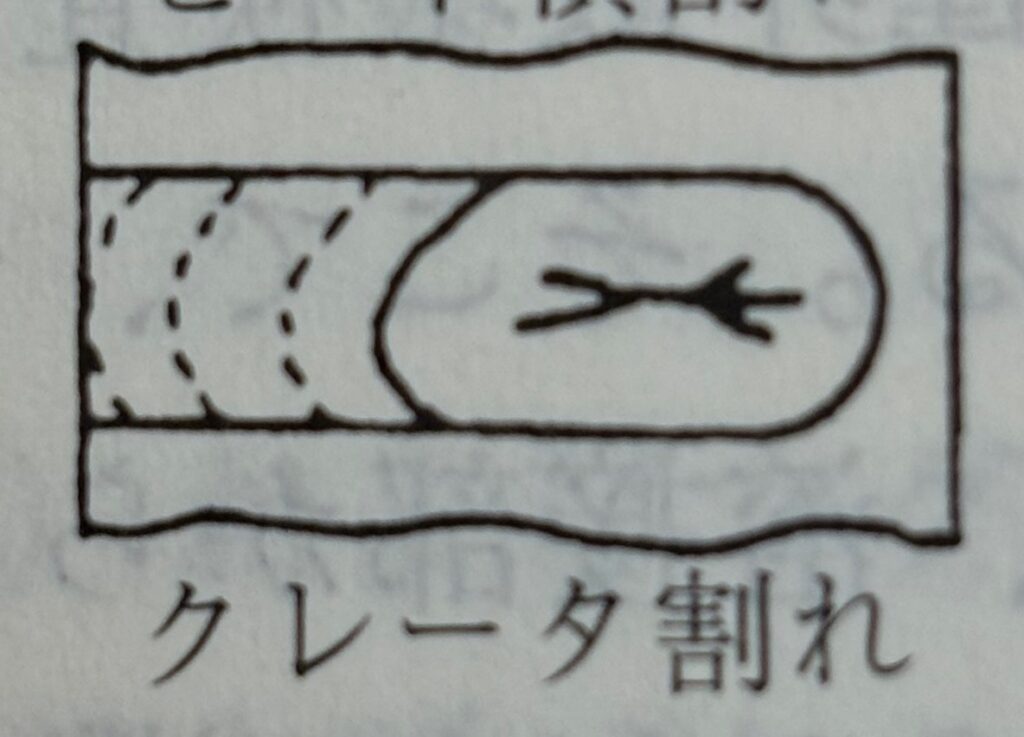
溶接ビードの終端部分で発生する割れ。クレーターと呼ばれる凹み部分に発生しやすいです。原因としては溶接の終了時に適切な溶融池の充填が行われず、急激な冷却によりクレーター部分に応力が集中して割れが発生します。
- 溶接終了時にクレーター部分を十分に充填する
- 終了時に電流を徐々に下げるタッチアップ技術を使う
- 溶接後の冷却をゆっくり行う
ビードルート割れ
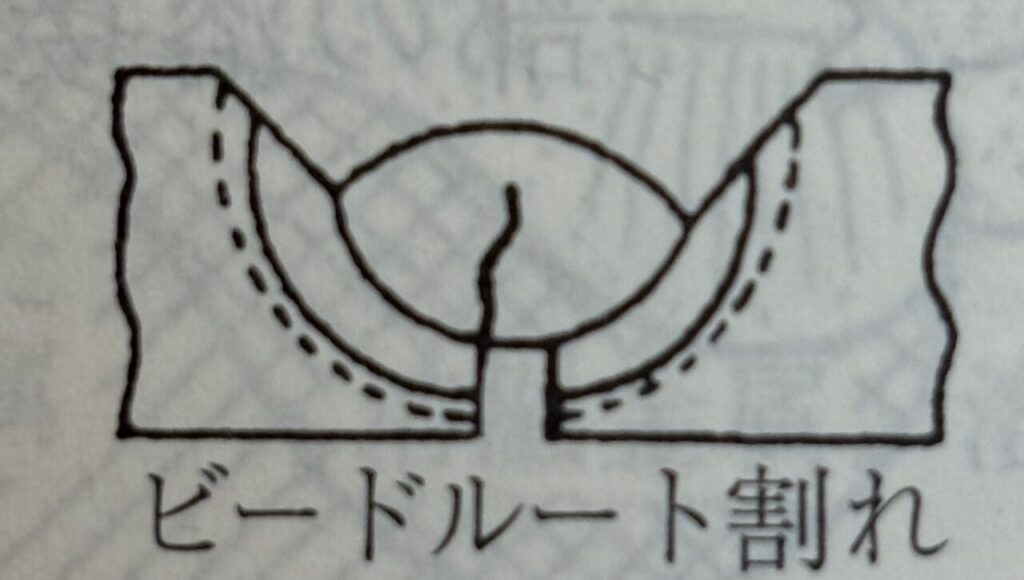
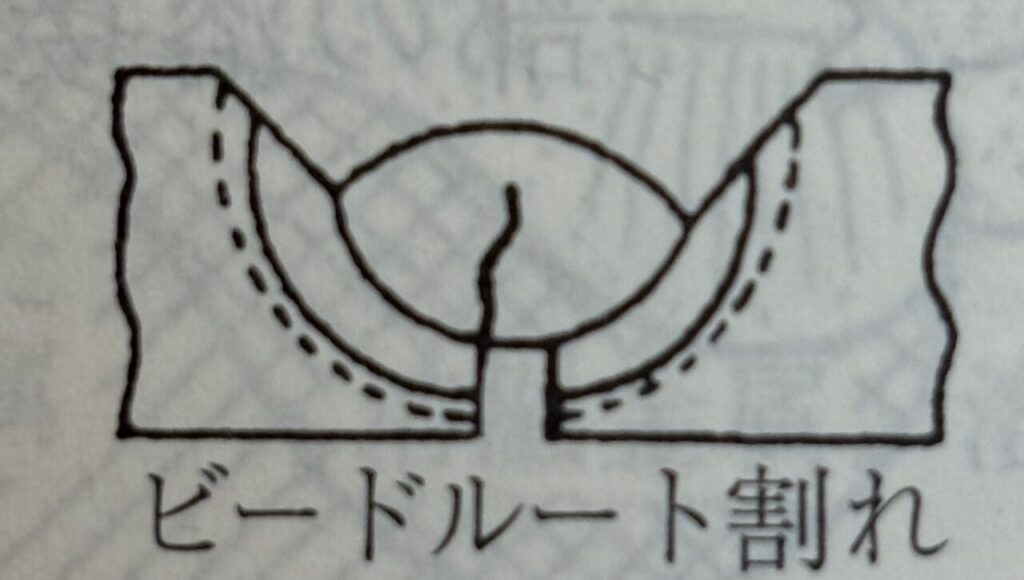
溶接ビードの根元部分(ルート)に発生する割れです。特に、突合せ溶接や隅肉溶接で問題となります。原因としてはルート部分が適切に溶け込まずに不完全な溶接が行われた場合や、応力が集中する形状で割れが発生します。また、過大な熱応力や不適切な溶接条件も影響します。
- ルート部への十分な溶融を確保する
- 適切な溶接電流と溶接速度の選定
- ルート部の準備やギャップ管理を適切に行う
サブマージアーク溶接の凝固割れ
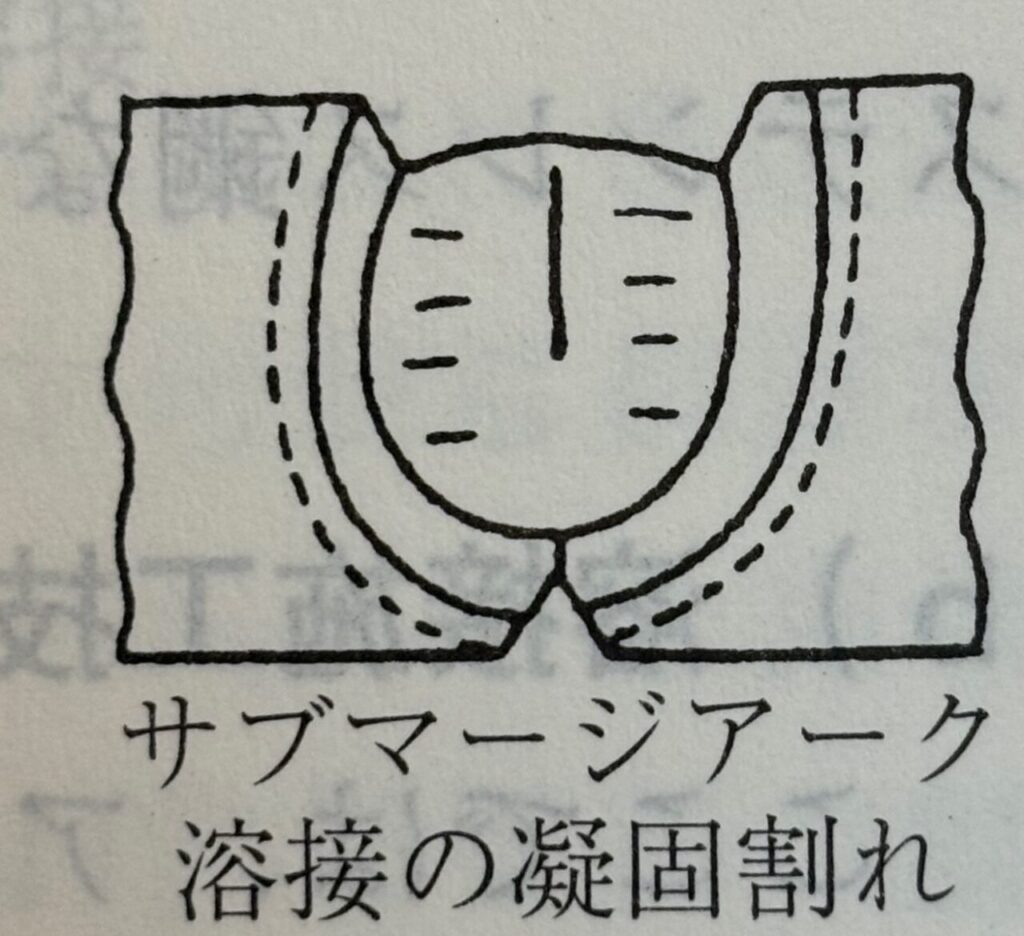
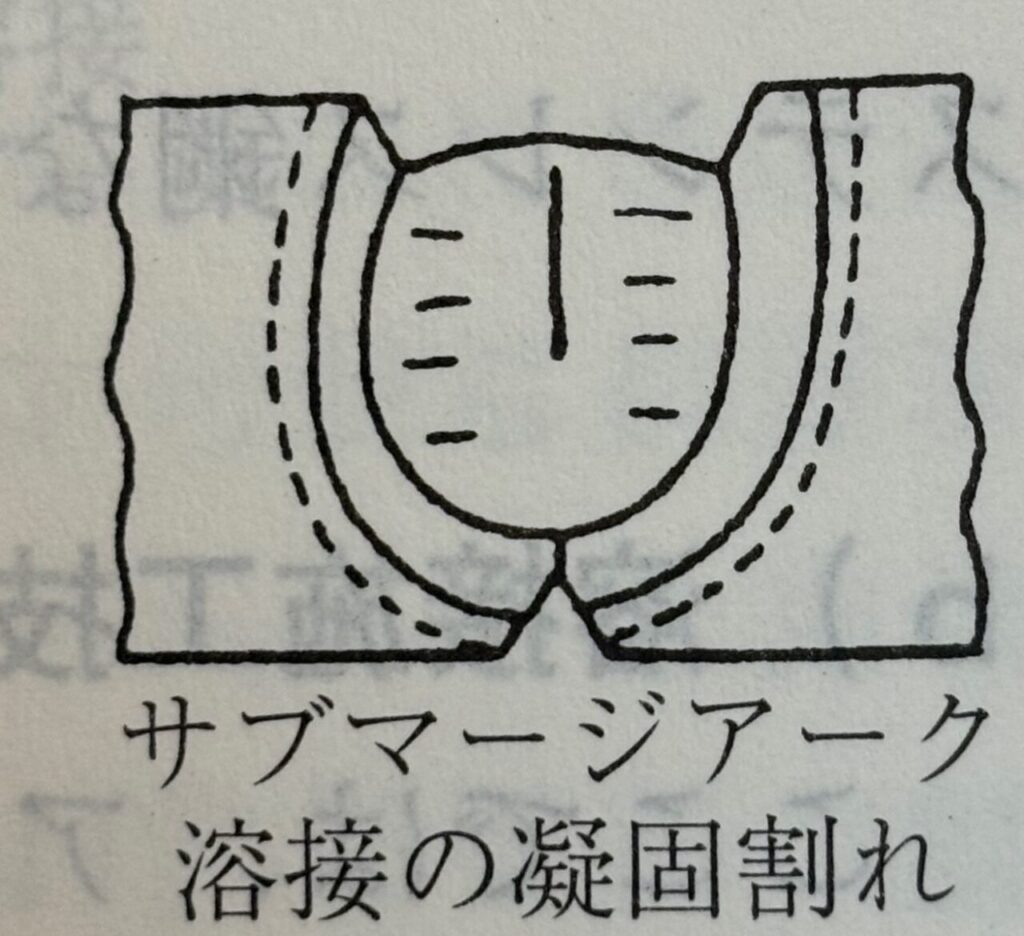
サブマージアーク溶接時に、溶融金属が冷却・凝固する過程で発生する割れです。原因として溶融金属が急速に凝固する際に、金属内部に引張応力が生じ、これが臨界値を超えると割れが発生します。特に合金元素が多い場合や、過度な溶接条件が凝固割れを促進します。
- 溶接材料の選定時に、合金成分を考慮して割れの発生を抑える
- 予熱や後熱処理を適切に行う
- 溶接条件(電流、速度、電圧)を調整して凝固速度を制御する
隅肉ビードルート割れ
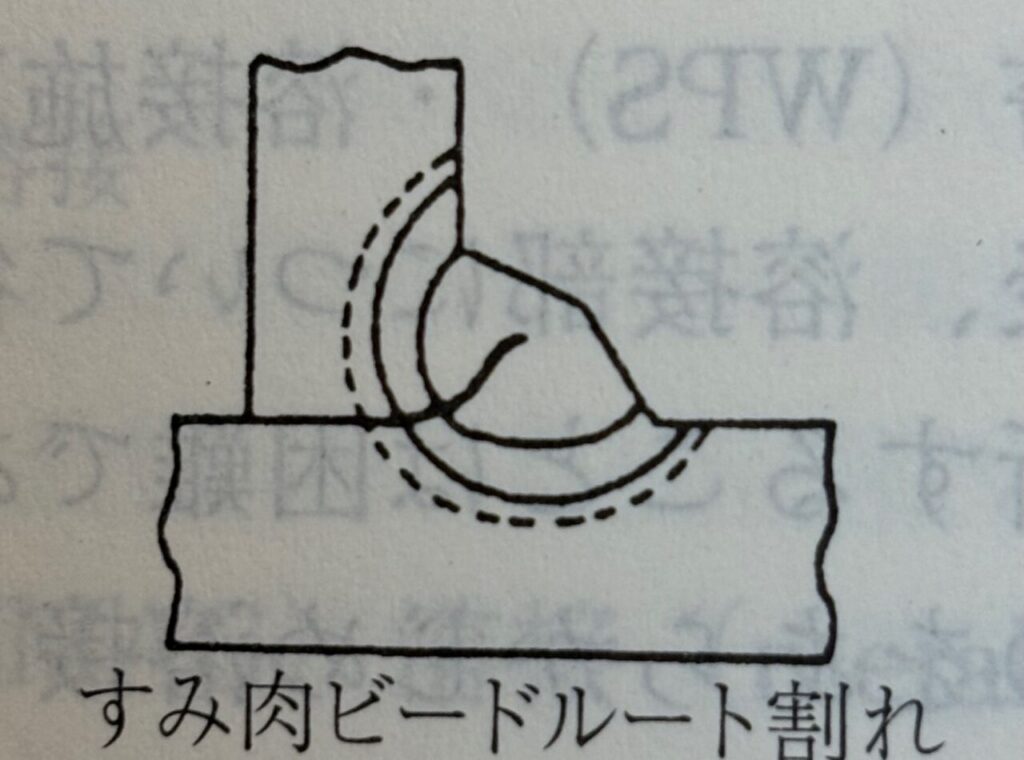
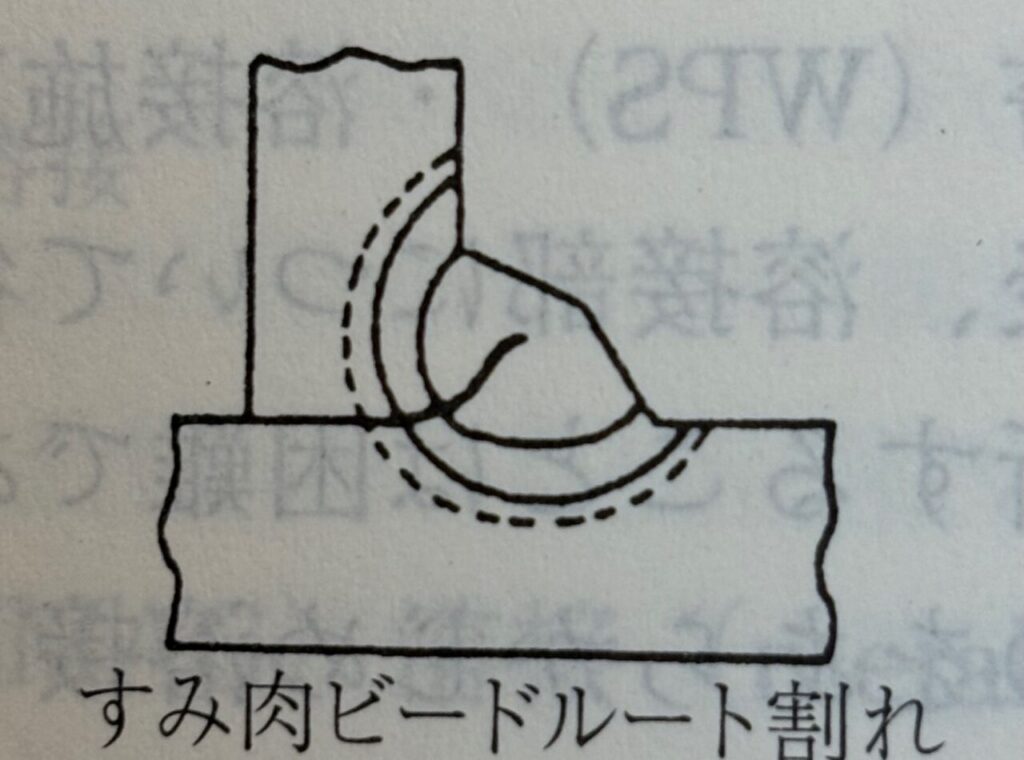
隅肉溶接で、溶接ビードのルート部分に発生する割れです。特に、応力が集中するコーナー部分で発生しやすいです。原因として溶接部位の形状や溶接金属の不適切な溶け込みによる応力集中が主な原因です。また、熱応力や冷却速度の不均一も影響します。
- 適切な溶接条件(電流、速度、電圧)の設定
- ルート部の十分な溶け込みを確保する
- 溶接方法や順序を最適化し、応力集中を避ける
低温割れ
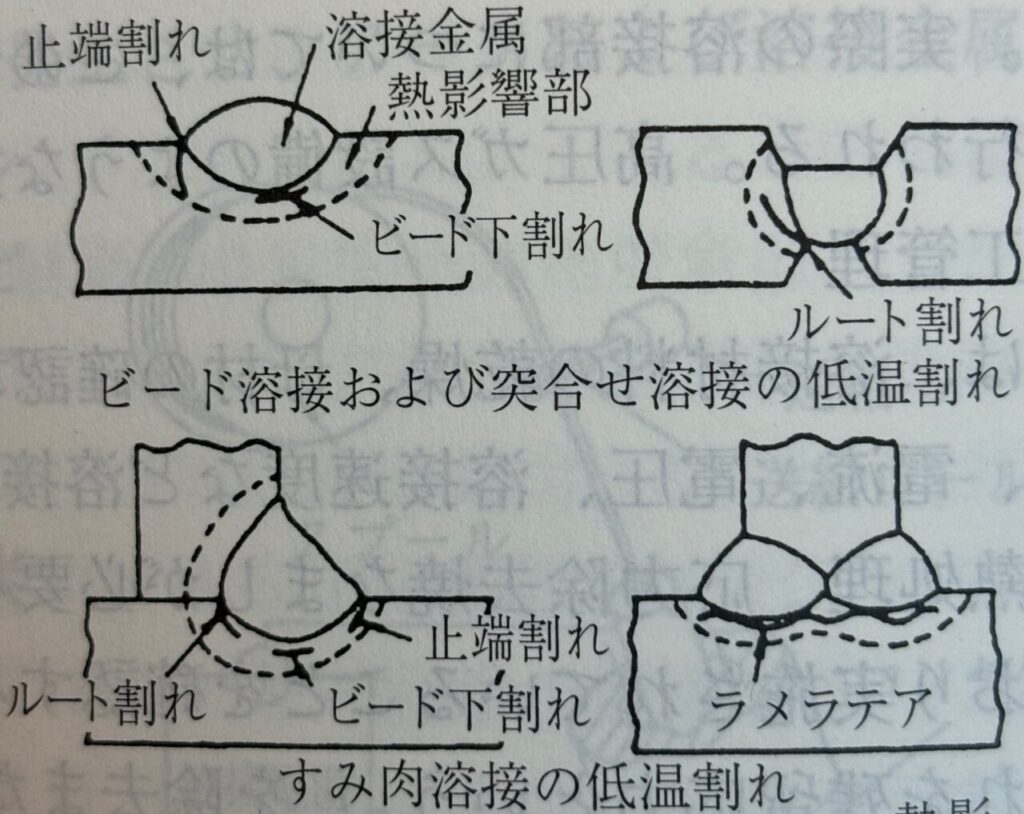
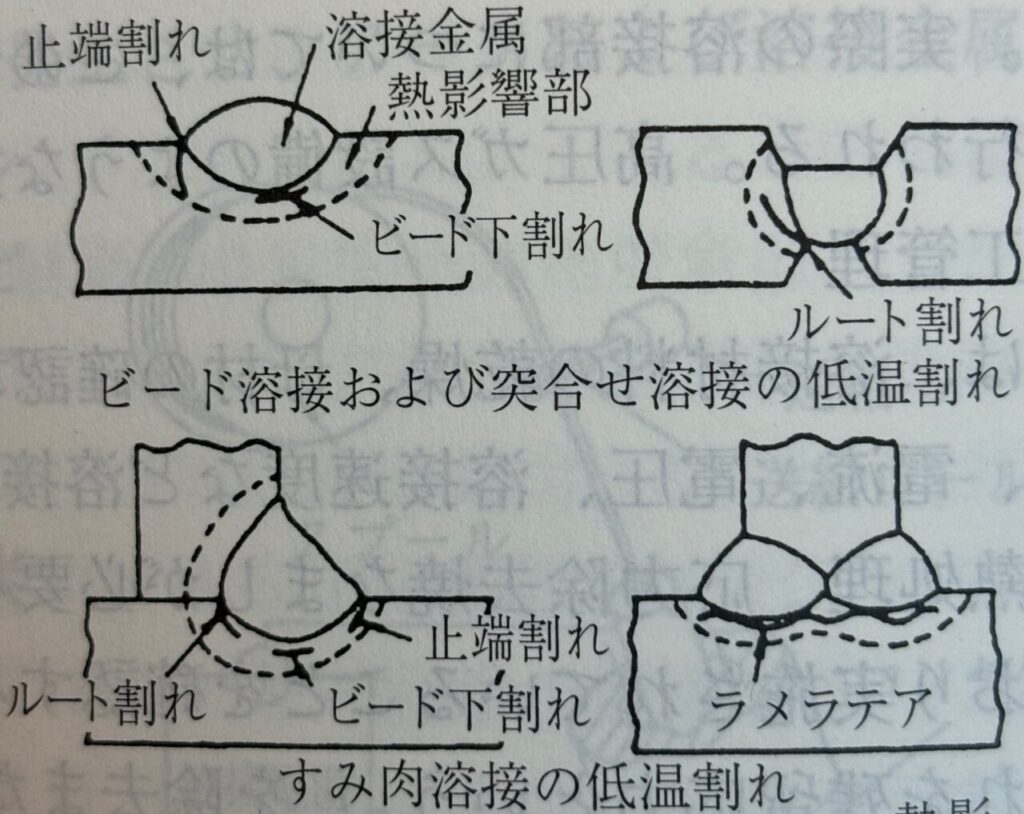
溶接部が低温状態で割れる現象で、通常は溶接後の冷却過程で発生します。水素脆性やマルテンサイト変態などが関与する場合が多いです。原因として溶接時に侵入した水素が、冷却中の金属の中で脆化を引き起こし、割れを発生させます。また、急速な冷却によって発生するマルテンサイト組織も脆性を引き起こすことがあります。
- 予熱や後熱処理を適切に行い、水素の拡散を防ぐ
- 低水素系溶接材料を使用する
- 冷却速度を制御し、ゆっくり冷却する
高温割れ
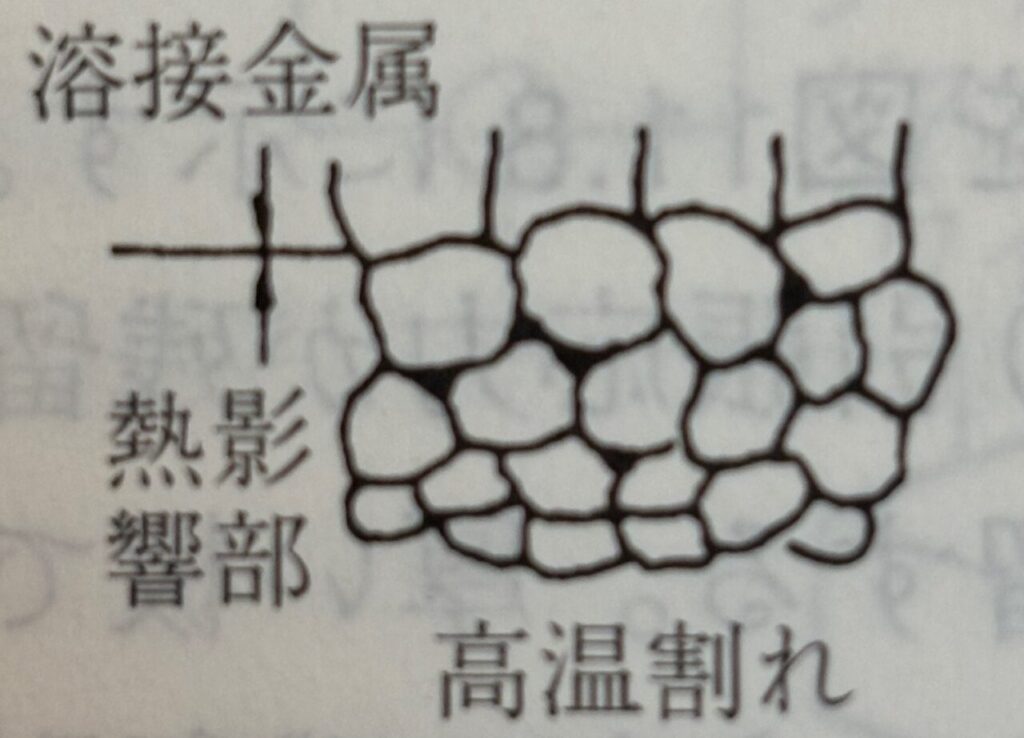
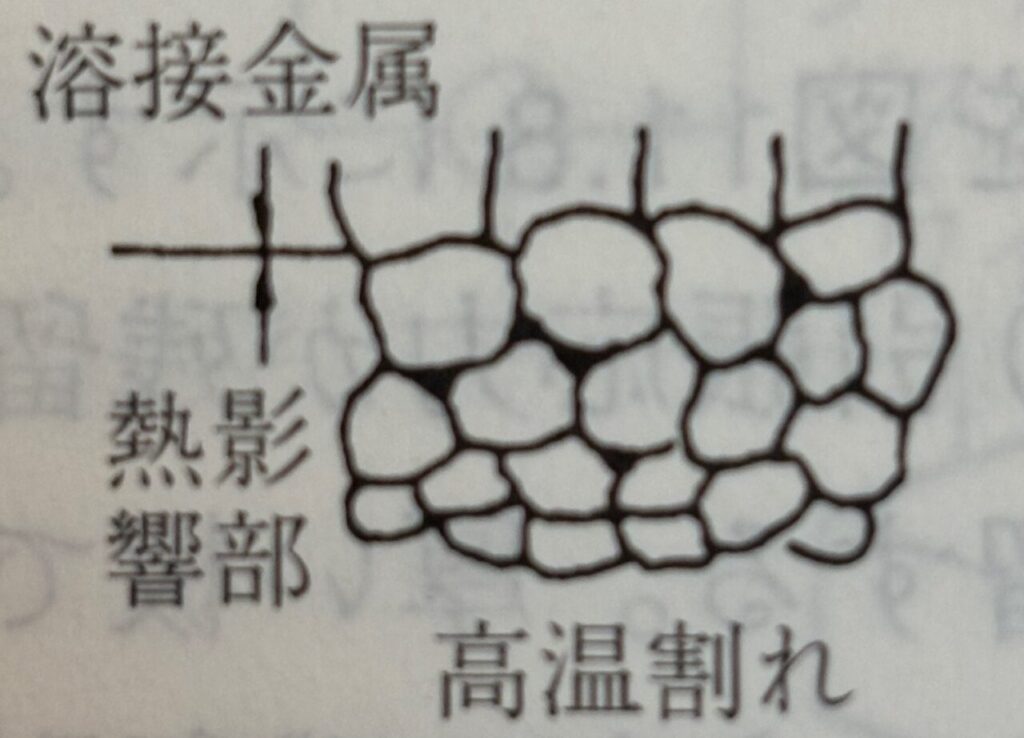
溶接金属が高温のままで割れる現象です。通常は溶接中やすぐ後に発生します。原因としては溶接中の高温で金属が脆くなることに加え、溶接金属の不均一な冷却によって内部応力が発生し、これが原因で割れが生じます。特に、高温脆化しやすい合金で発生しやすいです。
- 溶接温度管理を徹底し、適切な温度で作業を行う
- 適切な溶接材料を選定する
- 予熱と後熱処理を行い、応力を軽減する
これらの割れは、それぞれ異なる原因で発生するため、対策も異なりますが、共通して言えるのは、溶接条件の最適化と、適切な予熱・後熱処理、適切な溶接材料の選定が重要であるということです。
溶接欠陥の原因
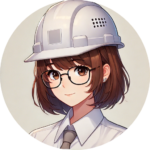
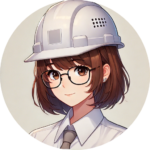
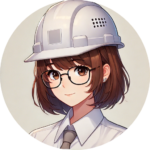
でも結局欠陥って製作時に発生するから製作側で気をつければいいのでは?
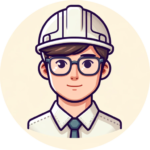
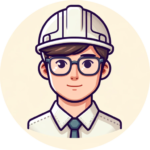
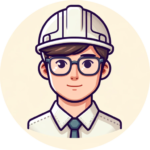
確かにそうだね。でも製作側で欠陥が起きないように適切な溶接指示をすることも必要だよ
溶接欠陥が発生する原因は複数の要因に分けられます。ここでは、技術的要因、材料的要因、環境的要因に分けて解説します。
技術的要因
不適切な溶接技術は、最も一般的な欠陥の原因となります。以下は主な技術的要因です。
- 溶接速度: 速すぎる溶接速度はアンダカットや融合不良を引き起こす可能性があります。逆に、遅すぎる速度は過度な溶接金属の蓄積やオーバーラップを引き起こします。
- 電流・電圧の管理: 適切な電流・電圧の選定が行われないと、溶接品質が大きく損なわれます。高すぎる電流は、過溶融やアンダカットの原因となります。
- 溶接者の技術: 溶接技術者のスキルが低い場合、溶接ビードが不均一になり、外観や内部に欠陥が生じる可能性が高まります。
材料的要因
材料そのものの性質や管理不良も溶接欠陥の原因となります。
- 材料の不適合: 特定の材料は、他の材料よりも溶接欠陥が発生しやすい傾向があります。例えば、オーステナイト系ステンレス鋼やアルミニウム合金は高温割れが発生しやすいです。
- 表面汚染: 材料の表面に油や汚れが付着していると、気孔やスラグ巻込みが発生しやすくなります。溶接前のクリーニングは欠かせません。
環境的要因
溶接作業が行われる環境も、欠陥の発生に大きな影響を与えます。
- 風や湿度: 屋外での作業や湿気の多い環境では、ガスシールドが不十分となり、気孔が発生しやすくなります。また、溶接中の風はシールドガスを吹き飛ばす原因となります。
- 温度管理: 溶接時に適切な温度管理が行われない場合、冷却速度が異常となり、低温割れや高温割れが発生しやすくなります。
溶接欠陥の防止策
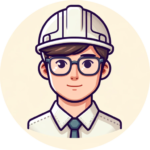
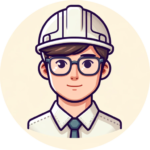
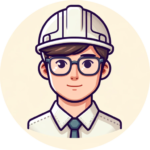
じゃあ実際にどうやって欠陥を防ぐかみていこう。準備を適切にすれば欠陥を防ぐことは可能
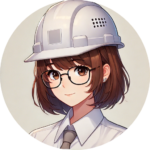
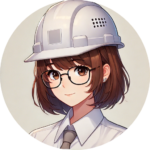
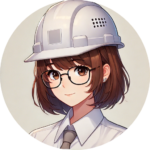
段取り8分ってことですね!
溶接欠陥を未然に防ぐためには、適切な管理と準備が必要です。以下に主な防止策を紹介します。
適切な溶接技術の使用
溶接速度、電流、電圧などのパラメータは、溶接される材料や作業環境に応じて慎重に設定されるべきです。また、溶接者は十分なトレーニングを受け、品質管理のための定期的なスキル向上が求められます。
材料の適切な準備
溶接に使用する材料は、事前に適切な準備がなされるべきです。特に、材料の表面は清潔に保ち、油や汚れを徹底的に取り除くことが重要です。さらに、必要に応じて前加熱を行い、材料の内部応力を緩和することで、割れの発生リスクを低減します。
溶接後の処理
溶接が完了した後、適切な熱処理を施すことで、溶接部の残留応力を軽減し、割れの発生リスクを抑えることができます。特に、熱影響部の金属組織を安定化させることが目的です。
環境の制御
作業環境は、欠陥の発生を防ぐために重要です。風や湿気の多い環境では、シールドガスの供給が安定するように工夫し、シールドガスが外部に流れ出さないように管理します。また、温度管理も重要で、特に低温環境では適切な加熱処理を施すことで、低温割れを防ぐことができます。
使用中に発生する溶接欠陥
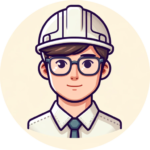
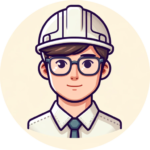
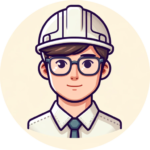
ただ残念なことに使用中に欠陥が発生することもある
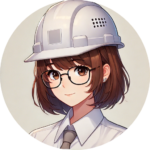
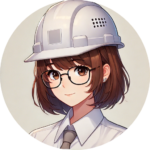
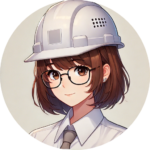
使用中の発生だと設計、製作側でも防ぐのは難しそう・・・
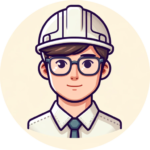
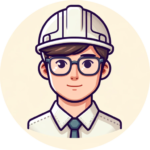
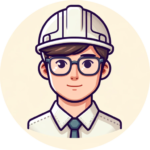
こういう時は使用状況をしっかりと把握して設計段階で対応することがまず重要。さらに製作側に適切な溶接方法も指示することが重要だよ!
溶接欠陥は、製造時だけでなく、使用中に発生する場合もあります。例えば、圧力や温度の変動が繰り返し起こる環境では、溶接部が疲労することで「疲労割れ」が発生しやすくなります。また、ステンレス鋼などの材料は、長期間の使用によって「粒界腐食」が進行しやすく、これが溶接部に欠陥を引き起こすことがあります。
- 疲労割れ: 溶接部が繰り返しの応力により劣化し、亀裂が発生する現象。主に機械的負荷がかかる部分に発生します。
- 粒界腐食: ステンレス鋼の熱影響部で発生する現象で、腐食が進行することで材料の強度が低下し、割れや剥離が生じます。
溶接部の欠陥の検査
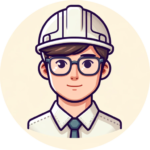
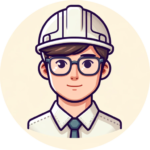
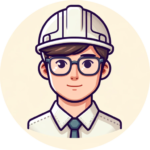
実際に欠陥を検査する方法もいろいろあるよ。別記事で解説しているのでみていってね。
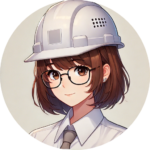
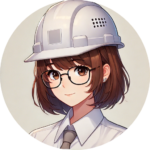
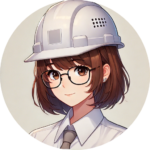
製作したものを曲げ試験機にかけるわけにもいきませんからね!
溶接部の欠陥の検査は基本的には非破壊検査で行われます。溶接方法の有効性や強度試験に関しては曲げや引っ張り試験を行いますが、製作した製品を破壊するわけにはいきません。
そのため、目視検査や浸透探傷試験などの非破壊検査を行います。非破壊検査に関しては「【壊さずに検査】非破壊検査の概要とその種類について解説!」を参考にしてください。
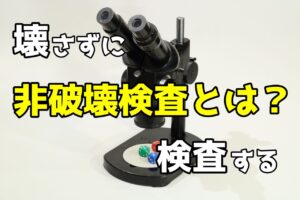
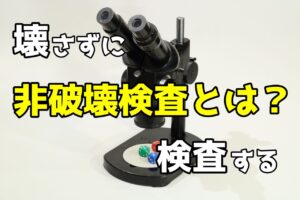
各種欠陥に対しての検査方法は以下の画像のようになります。間違った方法だと欠陥を検出することができないので、注意しましょう。
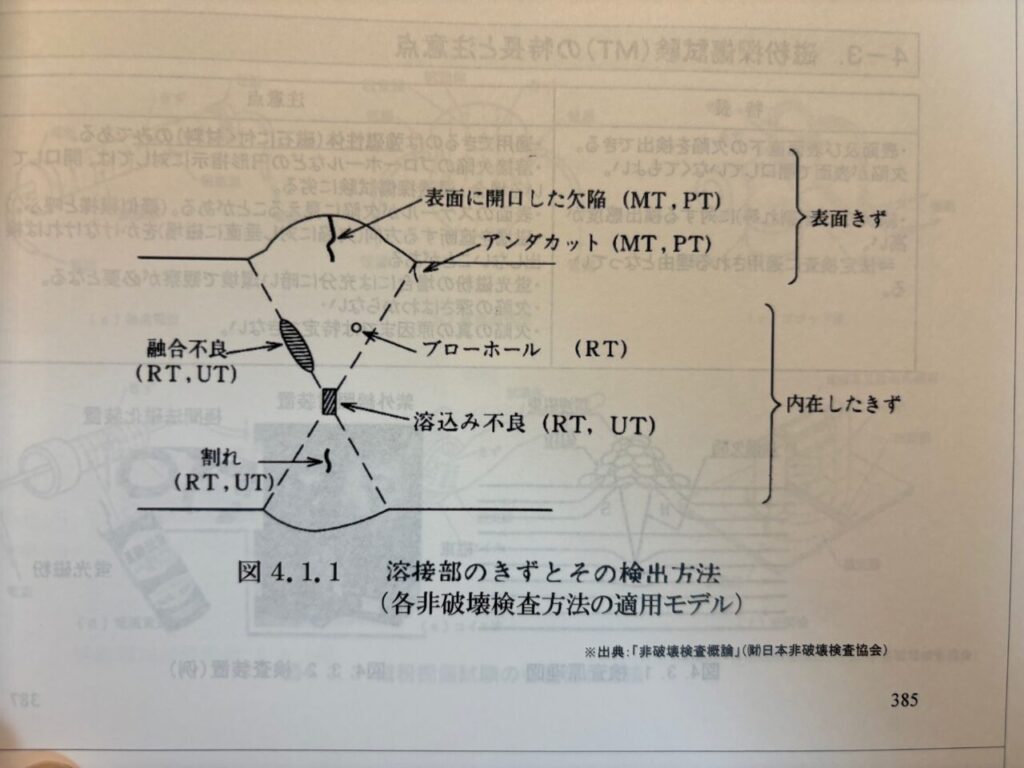
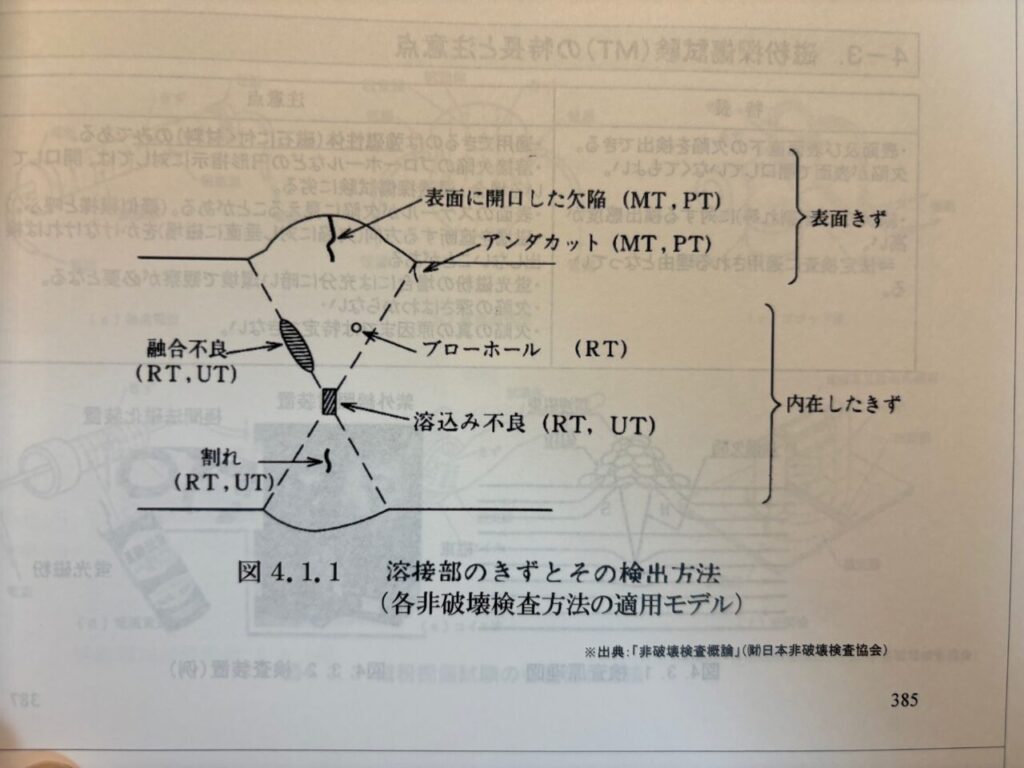
まとめ
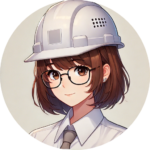
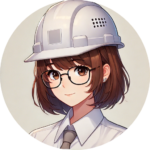
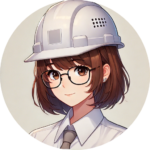
溶接欠陥も非常に奥が深い世界ですね・・・
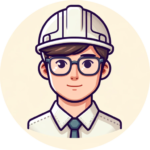
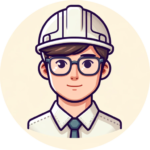
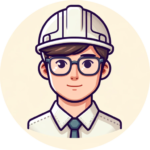
そうだね。でも溶接は母材と同等の強度が期待できるし、リベットやボルトナットよりも手軽に施工できる。タンクなんかは溶接じゃないとほぼ製作不可能だよね?なので事故を起こさないようにしっかりと理解しよう
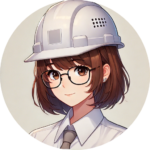
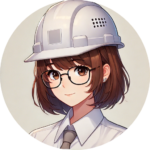
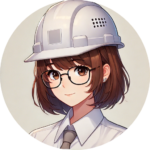
欠陥の検査方法も合わせて覚える必要がありますね!
溶接欠陥は、プラント機器や機械設備の性能や安全性に大きな影響を与える重要な課題です。欠陥には外観的なものから内部に隠れたものまでさまざまな種類が存在し、その原因も多岐にわたります。技術的、材料的、環境的な要因が重なり合って欠陥を引き起こすため、溶接作業には細心の注意が必要です。
欠陥の発生を防止するためには、適切な溶接技術の使用、材料の準備、環境の管理、そして製造後の検査や熱処理が不可欠です。また、使用中に発生する欠陥にも十分な対策が必要であり、定期的なメンテナンスや検査によって製品の寿命を延ばすことが求められます。
溶接は高度な技術であり、その品質管理が製品の信頼性を大きく左右します。溶接欠陥のリスクを最小限に抑え、より高品質な製品を提供するために、技術者や製造業者は常に最新の技術と知識を習得し、実践していくことが求められます。
コメント