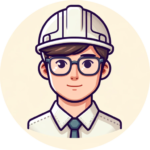
溶接はプラント配管だけでなく多くのところで使われているからよく理解する必要があるよ
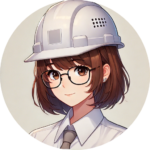
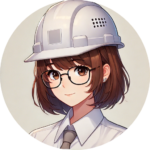
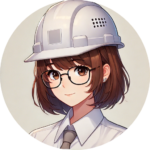
でも金属を溶かしてくっつけるだけでしょ?どっちかというと製作側の方が気をつけるべきじゃない?
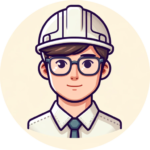
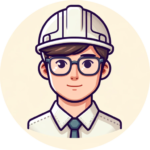
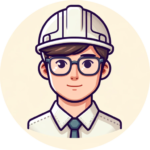
そんなことはないよ!溶接方法だけでなく開先などもきちんと設計しないとトラブルにつながるよ!
溶接施工は、現代の多くの産業分野において欠かせない技術です。建築や自動車製造、造船、圧力容器の製造など、さまざまな分野で広く使用されており、その正確さと信頼性は製品の品質を左右します。この記事では、溶接の基本的な概念や種類、そしてそれぞれの溶接方法の特徴について解説します。
溶接とは?
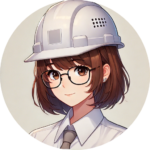
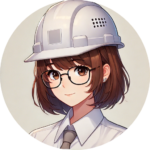
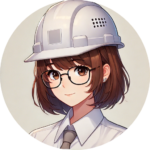
そもそも溶接って何??
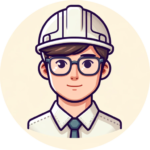
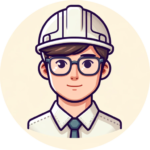
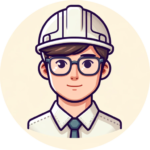
イメージは”溶かして接合”だけどそれ以外もあるよ
溶接(Welding)とは、2つ以上の部品を接合するための技術であり、接合部分を熱や圧力を利用して一体化させる方法です。リベット継手やフランジ継手などの機械的な接合方法と並び、工業的に重要な位置を占めています。
溶接は主に以下の3つの方法に大別されます。
融接法:接合部分を溶かして接合する方法
圧接法:熱と圧力を用いて接合する方法
ろう付け:接合部分よりも低い融点の金属を溶かして接合する方法
これらの方法のうち、特に「融接法」が広く用いられており、建設や製造業での溶接施工において主流の手法となっています。
融接法の概要
融接法は、接合部分を高温に加熱して溶融し、冷却して一体化させる溶接方法です。必要に応じて溶融金属を供給し、自然冷却させることで接合が行われます。この過程で、接合された部分は「溶接金属」と呼ばれ、特定の機械的性質を持つ鋳造組織が形成されます。
熱影響部(HAZ)とは?
融接法では、接合部の近くにある材料も熱の影響を受け、その機械的性質が変化します。これを熱影響部(Heat Affected Zone, HAZ)と呼びます。HAZの特性は溶接の品質に大きく影響を与えるため、適切な管理と技術が求められます。
アーク溶接はこの融接法の一種であり、圧力容器や建築構造物、造船など、幅広い分野で利用されています。アーク溶接はその手軽さと強度のバランスが良く、特に高強度を必要とする場面で広く採用されています。
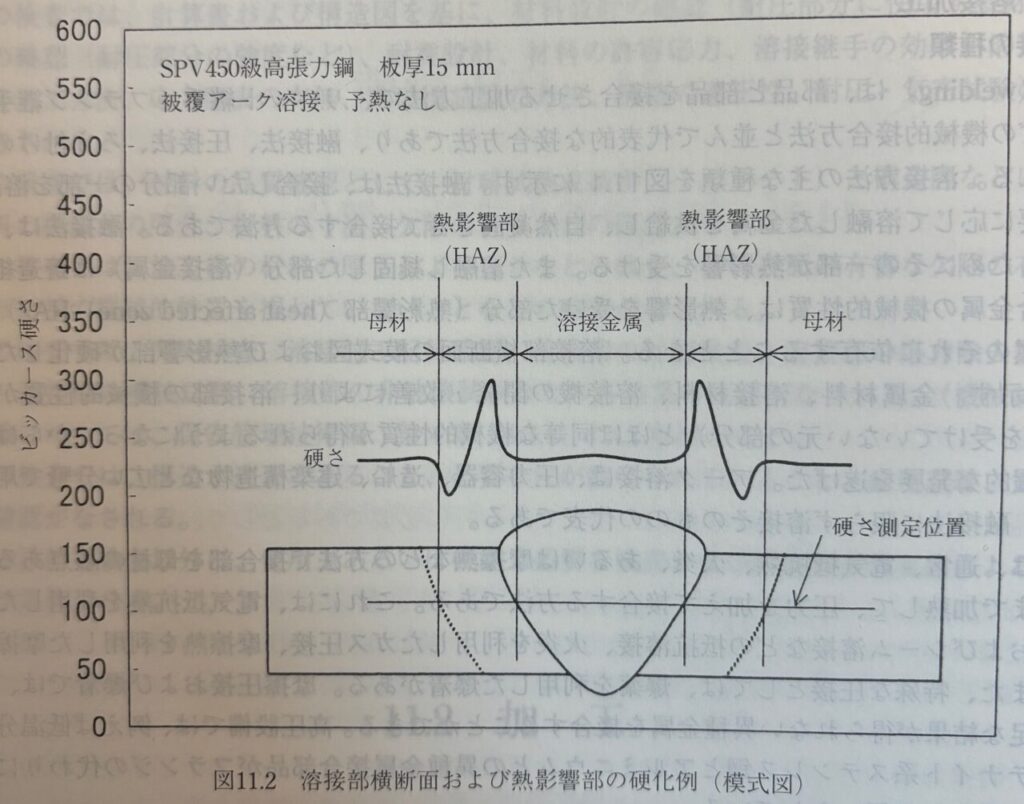
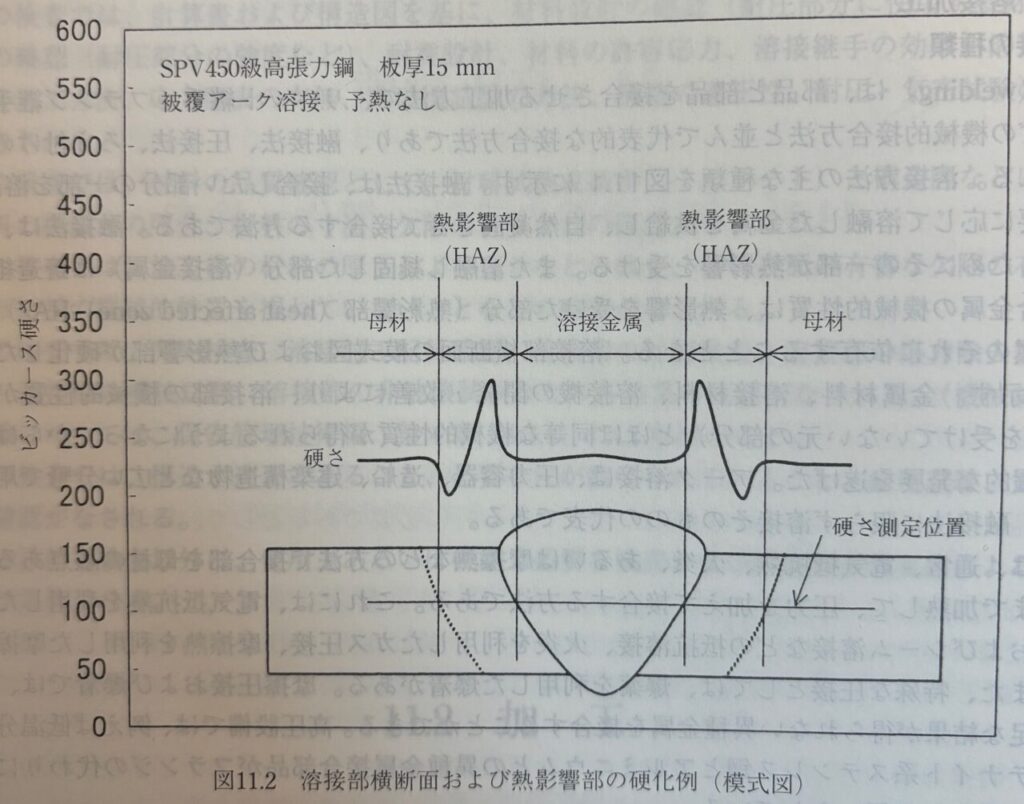
圧接法の特徴
圧接法(Pressure Welding)は、接合部分を加熱し、圧力を加えて接合する方法です。接合には、電気抵抗や火炎、摩擦などの熱源を使用します。圧接法の代表的な手法には以下があります。
- スポット溶接:電気抵抗による接合
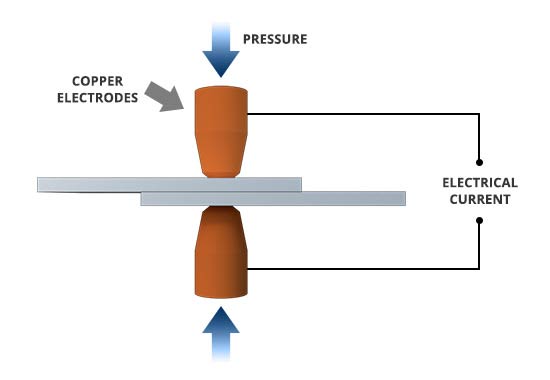
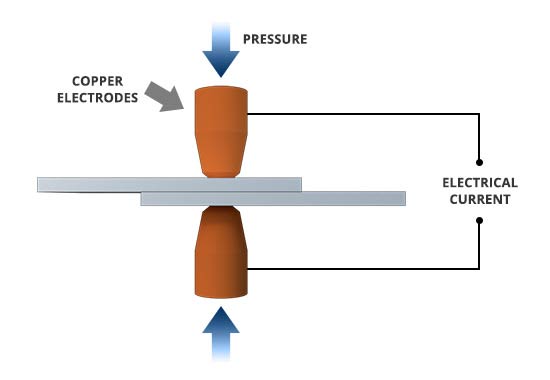
- シーム溶接:電気抵抗による継続的な接合
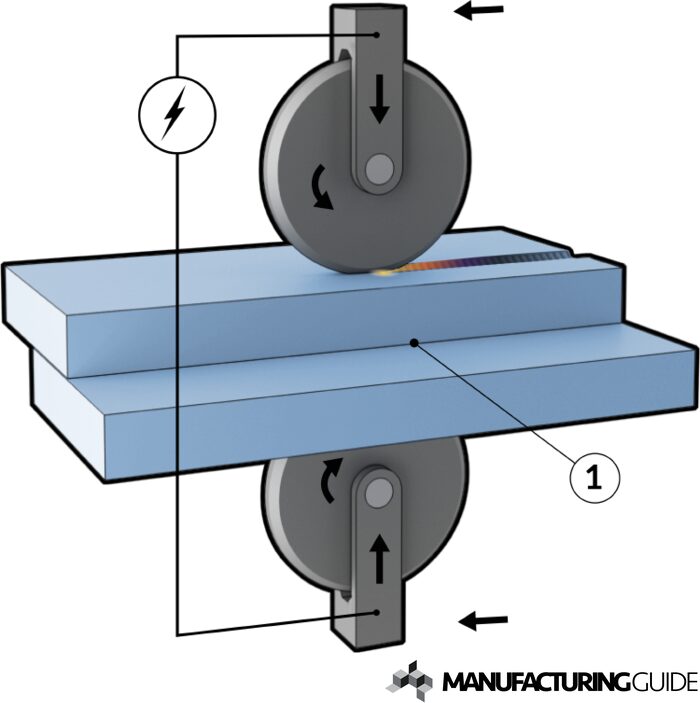
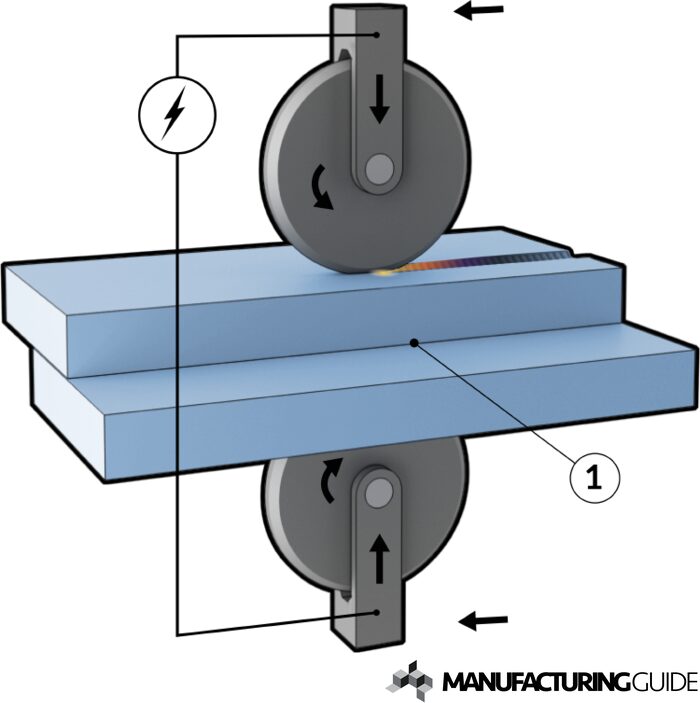
- ガス圧接:火炎を利用した接合
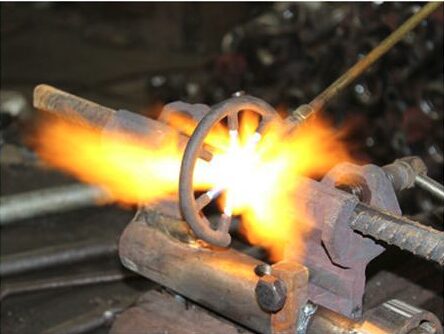
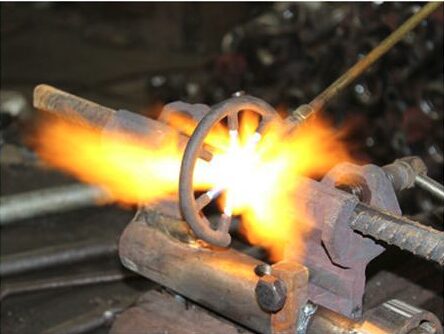
- 摩擦圧接:摩擦熱を利用した接合
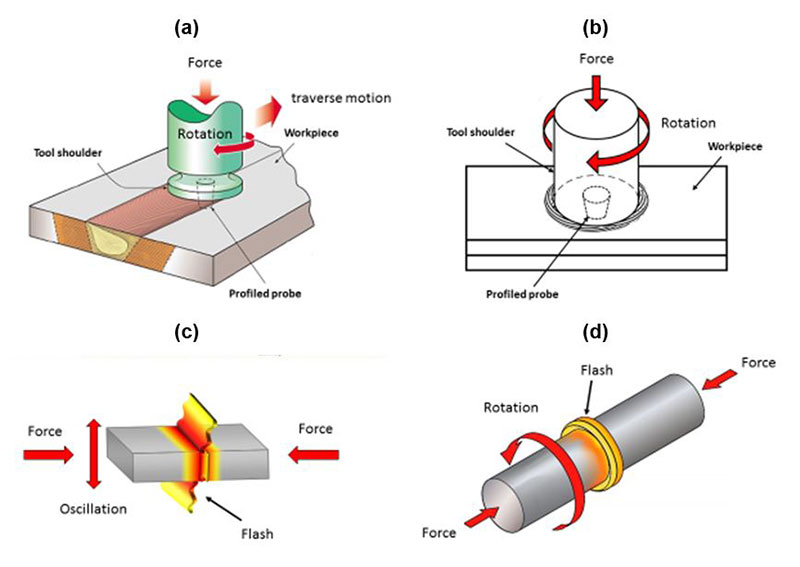
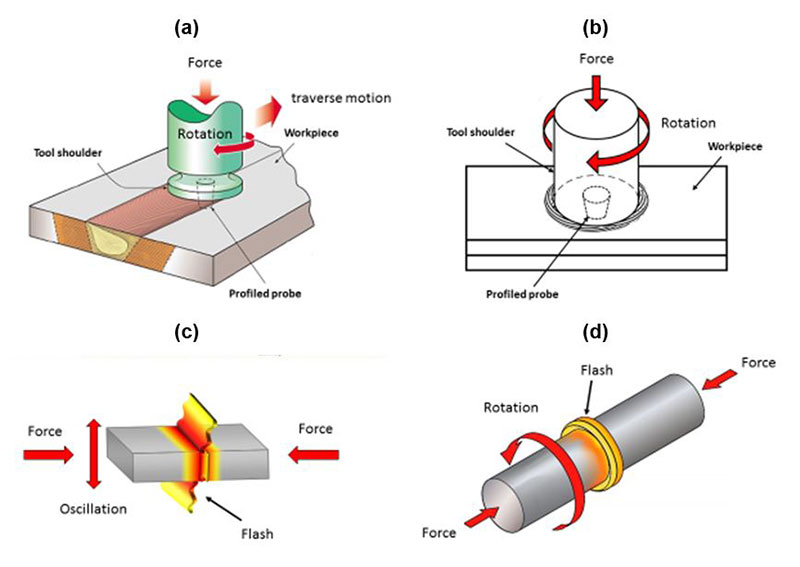
圧接法は、融接法では接合が難しい異種金属同士を接合する際にも効果的です。例えば、低温環境下での設備や異なる金属の接合が必要な場面では、圧接法が優れた結果をもたらします。
ろう付け
ろう付け(Brazing)は、母材よりも低い融点を持つ金属(ろう材)を使用して接合する方法です。この方法は、接合時の温度が母材よりも低いため、材料に対する熱の影響が少なく、細かい部品や複雑な構造物の接合に適しています。
ろう付けは融点の違いにより、次の2つに分けられます。
- 硬ろう付け:銀ろう付けが代表例で、高温での接合に適する。
- 軟ろう付け:はんだ付けが代表的で、低温での接合に使用される。
また、特殊なろう付け技術として、真空ろう付けがあります。これは、アルミニウム合金やステンレス鋼の熱交換器などの製造に多く用いられており、気密性が求められる製品に適しています。
ガス溶接
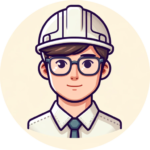
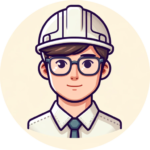
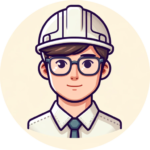
まずはガス溶接これは溶接だけでなく切断にも使われるね
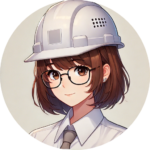
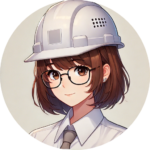
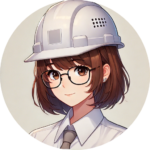
アセチレンと酸素を使うやつですね!
ここからは融接法で使用される溶接法について解説していきます。融接法は産業界でも幅広く使用されているので、それらの方法を理解して適切な方法で溶接施工できるようにしましょう。
まずはガス溶接からです。
1. ガス溶接とは
ガス溶接は、可燃性ガスの燃焼熱を利用して金属を接合する方法です。最も一般的な形態は酸素-アセチレンっを使用する方法で、これはアセチレン(C₂H₂)と酸素(O₂)を組み合わせて高温の炎を生成し、その熱によって金属を溶かして接合します。
この手法は、比較的低い温度で溶接が行えるため、熱に弱い材料や薄板の加工に適しています。
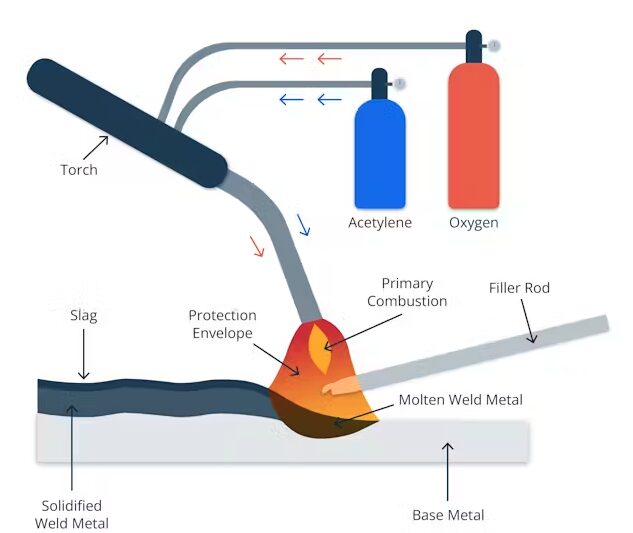
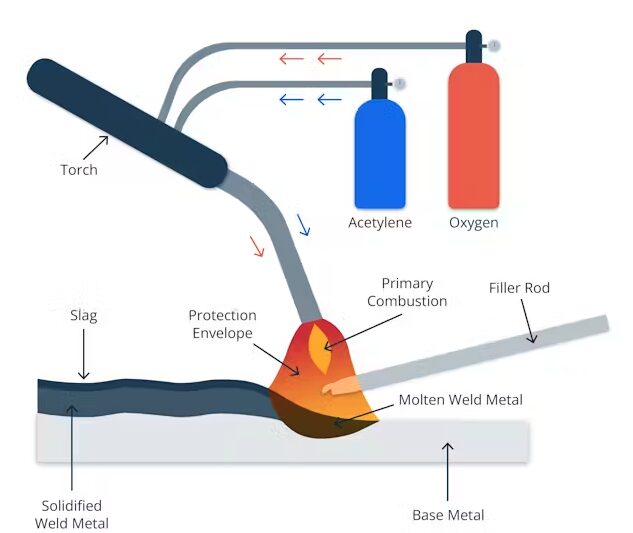
2. ガス溶接の特長と利点
ガス溶接は、以下のような特長があります。
- 低い温度での加熱: ガス溶接では、アーク溶接に比べて火炎の温度が低いため、熱影響部の範囲が大きくなることがありますが、その分、材料に対する割れ感受性が小さく、比較的繊細な作業に適しています。
- 調整の容易さ: 炎の温度や強度を細かく調整できるため、溶接の際のコントロールがしやすいです。
- 適用範囲: 特に融点の低い材料や、薄板、そして修理作業に向いています。
3. ガス溶接の種類
ガス溶接では、火炎の種類によって作業の適性が異なります。特に、酸素とアセチレンの混合比率に応じて以下の3つの火炎が生じます。
- 中性炎: 酸素とアセチレンが同量の場合、最もバランスの取れた火炎です。酸化も還元も行わないため、一般的な金属溶接に使用されます。
- 炭化炎(選炎): アセチレンが多い場合、金属に還元作用を与え、酸化を防ぐことができますが、鉄鋼などの材料には不向きです。
- 酸化炎: 酸素が多い場合で、酸化作用が強く、銅や黄銅などの材料に使用されます。
4. ガス溶接のデメリット
ガス溶接にはいくつかのデメリットも存在します。
- 低い能率: アーク溶接に比べて火炎の温度が低いため、熱の集中が悪く、溶接効率が劣ります。
- 熱影響部が広い: 炎が材料全体に及びやすいため、溶接部分以外にも熱が伝わり、熱変形が起きやすいです。
これらの理由から、現在ではガス溶接は一部の特殊な用途を除き、使用頻度が低下しています。
5. ガス溶接に使用される材料と規格
ガス溶接で使用される材料についてもJIS規格が定められています。代表的なものとして、以下の溶接棒が規定されています。
- JIS Z 3201: 軟鋼用ガス溶接棒
- JIS Z 3202: 銅および銅合金用ガス溶接棒
これらの溶接棒は、材料に応じて選定する必要があり、適切な溶接棒の選択が溶接品質に大きな影響を与えます。
6. 他の溶接技術との比較
現代では、アーク溶接やレーザー溶接、さらには自動化されたロボット溶接など、より高効率で精度の高い技術が主流となっています。これにより、ガス溶接は一般的な工業用途ではほとんど使用されなくなりましたが、次のような場面ではまだ活躍しています。
- 薄板や細かい修理作業: 特に自動車修理や芸術品の制作など、微細な調整が必要な作業で使用されています。
- 学習用途: 初心者向けに溶接技術を学ぶための基本的な手法としても用いられています。
7. 安全面での注意点
ガス溶接は高温の火炎を使用するため、火災ややけどのリスクがあります。安全に作業を行うためには、次のような注意点を守ることが重要です。
- 適切な防護具の着用: 眼や皮膚を保護するためのゴーグルや防護服の着用が必要です。
- 換気の確保: ガス溶接では、一酸化炭素など有害なガスが発生するため、作業環境の換気を十分に行う必要があります。
- ガスの管理: ガスボンベの取り扱いや保管には注意が必要で、特に漏れや引火に対する防止策を徹底する必要があります。特にアセチレンは非常に危険なガスであるのでその管理(横倒しにしない)などは、厳重に管理する必要があります。
- 各種機器の点検:ガス溶接ではアセチレン、酸素用の減圧弁やトーチ、逆火防止機など多くの機器を使用します。安全の確保のためにもこれら機器は定期的に点を行いましょう。
8. ガス溶接まとめ
ガス溶接は、その柔軟性と手軽さから、特定の分野で今なお使用されていますが、現代の溶接技術と比較すると効率面で劣るため、用途が限定されています。しかし、熱影響を最小限に抑えたい場合や、材料の特性に応じて炎を調整しやすいという利点を活かし、特定の溶接作業においては重要な役割を果たし続けています。
アーク溶接
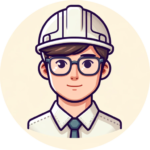
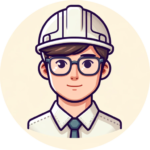
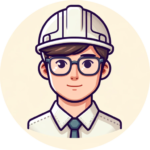
次はアーク溶接、こっちの方が一般的かな?
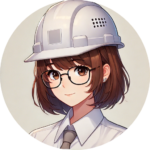
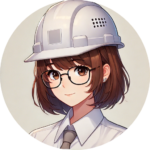
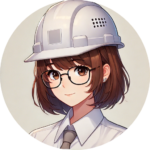
あのバチバチ火花飛ばしているやつですね!
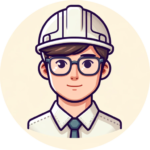
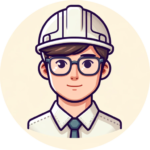
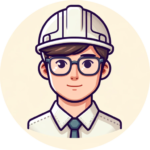
被覆アーク溶接はスパッタがすごいけどTIGはそこまでじゃないよ
アーク溶接とは、溶接の中でも最も一般的に使用される方法の一つです。この技術は、金属同士を接合するためにアークという高温の電気放電を利用します。
アークとは、電気がガス中を通過することで発生する放電現象の一種で、通常は大気圧以上の条件で発生します。このアークが金属表面に接触することで、高温によって金属を溶かし、溶融させることで接合を行います。
アーク溶接の特長は、高温度の熱源を容易に得ることができる点です。アークの温度は非常に高く、種類によっては約5000°Cから最大で50000°Cに達することもあります。この高温の熱によって、金属同士が確実に溶接され、強固な接合が実現します。
アーク溶接の種類
アーク溶接にはいくつか種類があります。これらは用途や材料によって使い分けられます。代表的なアーク溶接法として以下のものが挙げられます。
- 被覆アーク溶接(SMAW)
最も一般的なアーク溶接法で、溶接棒に被覆剤が付いた電極を用いてアークを発生させます。この方法は比較的シンプルで、さまざまな金属材料に対して使用できます。 - ガスシールドアーク溶接(GMAW)
溶接時にガスを吹き付けて空気を遮断することで、溶接部分を酸化させないようにする技術です。主にアルミニウムやステンレスなどの材料に使用されます。 - タングステンアーク溶接(TIG溶接)
非消耗性のタングステン電極を用い、手動で溶接棒を供給しながら行う溶接法です。主に薄い材料や高品質な溶接が求められる場面で使用されます。
アーク溶接のメリットとデメリット
アーク溶接には多くのメリットがありますが、デメリットもいくつか存在します。以下に主なポイントをまとめました。
メリット
- 高温度の熱源が容易に得られる
先述の通り、アークの温度は5000°C以上に達し、非常に高温です。これにより、さまざまな金属材料を確実に溶接することができます。 - 幅広い材料に対応可能
アーク溶接は、鉄、アルミニウム、ステンレス鋼など、多様な金属材料に使用することができます。 - 比較的安価な装置
アーク溶接に使用する機器は、他の溶接方法に比べて比較的低コストで購入可能です。
デメリット
- 高い技術が必要
アーク溶接は熟練した技術が求められる作業です。特に手動で行う場合、均一な溶接を行うためには経験が必要です。 - 作業環境が制限されることがある
屋外での作業では、風や雨などの影響でガスシールドが乱れることがあります。また、高温を発生させるため、作業者の安全対策も厳重に行う必要があります。
アーク溶接施工の基本手順
アーク溶接を行う際には、いくつかの基本的な手順を踏む必要があります。これらの手順を守ることで、安全かつ確実な溶接が可能になります。
- 材料の準備
溶接する金属表面を清潔に保ち、油分や酸化膜を除去します。また、溶接箇所の適切な位置決めも重要です。 - 電流と電圧の設定
使用する材料や溶接方法に応じて、溶接機の電流と電圧を調整します。これにより、アークの安定性と溶融量をコントロールします。 - アークの発生と維持
溶接電極と母材との間にアークを発生させ、そのアークを維持しながら作業を進めます。アークの長さや角度も重要で、これにより溶接の仕上がりが変わります。 - ビードの形成
溶接中は、溶融した金属が均一に流れるように注意しながら、ビード(溶接の跡)を形成します。ビードの形状や大きさは溶接強度に影響するため、慎重に作業を行います。 - 冷却と仕上げ
溶接が完了したら、溶接部を自然冷却させます。必要に応じて、溶接後の研磨や仕上げ処理を行い、見た目や強度を整えます。
アーク溶接における安全対策
アーク溶接は高温を扱う作業であるため、安全対策は非常に重要です。以下はアーク溶接において考慮すべき主な安全対策です。
- 適切な保護具の着用
溶接中は、強力な光や高温にさらされるため、適切な保護具(溶接ヘルメット、手袋、耐熱服)を必ず着用する必要があります。 - 作業場所の安全確保
周囲に可燃物がないことを確認し、風通しの良い場所で作業を行うことが推奨されます。また、消火器などの安全装置を近くに配置しておくことも重要です。 - 適切な換気
溶接時には有害なガスが発生することがあるため、作業場には十分な換気設備を設ける必要があります。
アーク溶接のまとめ
アーク溶接は、その高温による強力な接合能力から、さまざまな産業で広く使用されています。正しい技術と安全対策を守ることで、効率的かつ強固な溶接が可能です。これからアーク溶接を学ぶ人や、技術を向上させたいと考えている人にとっては、基本を理解し、実際の作業で経験を積むことが最も重要です。
アーク溶接の種類や手順を理解し、適切な方法で作業を行うことで、高品質な溶接施工が可能となります。
被覆アーク溶接とは?
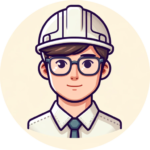
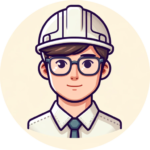
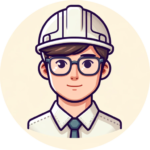
最も一般的な被覆アーク溶接。風に影響されにくいので屋外でも使えるよ!
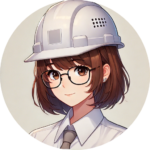
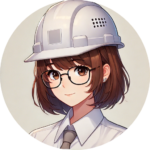
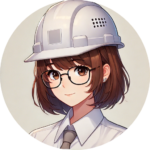
なのでビルの鉄骨の溶接とかにも使用されていますね
被覆アーク溶接(Shielded Metal Arc Welding, SMAW)は、金属の溶接に広く使用されている手動のアーク溶接法です。この方法は、溶接棒(電極)と溶接する母材の間に高温のアークを発生させ、その熱で金属を溶融し溶接を行います。
鉄鋼やステンレス鋼など、多くの金属に適用でき、建築や製造業など多岐にわたる分野で活用されています。
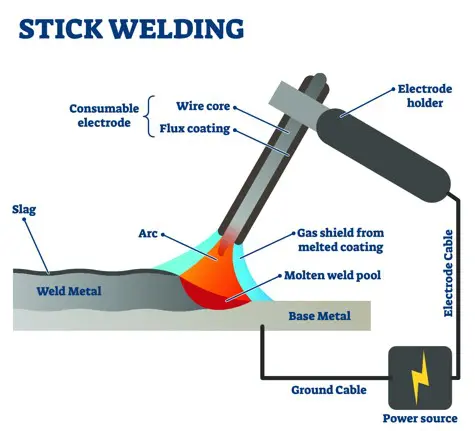
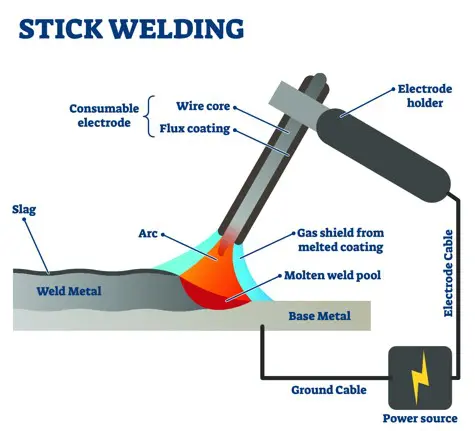
被覆アーク溶接の仕組み
被覆アーク溶接の基本的な仕組みは、以下の通りです。
- 溶接棒(電極)と母材の間にアークが発生します。このアークの温度は約6000℃に達し、その高温で金属が溶融します。
- 溶接棒の芯部は、母材と同様に適切な金属で構成され、その周りを覆う被覆剤(フラックス)が溶接の品質を向上させる役割を果たします。
- フラックスは溶接部を保護し、酸素の侵入を防ぐガスを発生させる他、溶融金属をスラグとして除去し、金属の成分を安定化させるための合金添加剤を含んでいます。
被覆アーク溶接の特徴
被覆アーク溶接は、他の溶接方法と比べて以下の特徴があります。
- 手軽さ:特殊な装置や高度な技術が不要で、溶接機と溶接棒があれば作業を開始できるため、比較的扱いやすい方法です。
- 高品質な溶接:適切な溶接条件下では、溶接部の機械的特性が良好で、強度や耐久性に優れています。
- 幅広い材料に対応:鉄鋼やステンレス鋼など、さまざまな金属に適用できる汎用性があります。
被覆アーク溶接の利点と欠点
利点
- コストパフォーマンスの良さ
被覆アーク溶接は、特別なガス供給設備が不要で、基本的な溶接機材のみで作業ができるため、比較的低コストで実施できます。 - 野外での作業が可能
フラックスが溶接部を保護するため、風や外部環境に左右されにくく、屋外での作業に適しています。特に建設現場や修理現場での使用に便利です。 - 多様なポジションでの溶接が可能
被覆アーク溶接は、上向き、下向き、横向きなど、さまざまな角度での溶接が可能です。これにより、作業現場での柔軟性が高まります。
欠点
- 熟練技術が必要
手動で行うため、技術者の経験やスキルにより、仕上がりの品質が左右されます。初心者には扱いが難しい場合もあります。 - スラグ除去の手間
フラックスが溶けて形成されるスラグ(溶融金属の不純物)は、溶接後に除去する必要があります。この作業に時間がかかる場合があります。
被覆アーク溶接の手順
被覆アーク溶接の一般的な手順は以下の通りです。
- 準備
母材の表面を清掃し、溶接部に付着した油や錆を除去します。 - アークスタート
溶接棒を母材に軽く接触させて短絡を発生させ、その後すぐに離してアークを形成します。これは「タッチスタート」と呼ばれる技術です。 - 溶接
アークを維持しながら、溶接棒を一定のスピードで移動させ、溶接部を形成します。この際、アークの長さを一定に保つことが重要です。 - スラグ除去
溶接が終わった後、スラグが表面に付着しているので、ハンマーやブラシを使用して除去します。
被覆アーク溶接のまとめ
被覆アーク溶接は、比較的簡便でコストパフォーマンスが良い一方、熟練した技術が求められる溶接方法です。屋外での作業や、様々な材料に対応できる点が評価され、多くの分野で活用されています。しかし、スラグの除去や一定の技術が必要な点に留意し、適切な溶接施工を行うことが重要です。
また、溶接の成功には、溶接機の選定やフラックスの選択が重要な要素となります。特にアークの安定性や材料の特性に応じた溶接棒を使用することが、最良の結果を得るための鍵となるでしょう。
被覆アーク溶接は、今後もさまざまな分野でその利用が拡大し続ける溶接技術の一つです。
Tig溶接とは?– 基本概念と特長
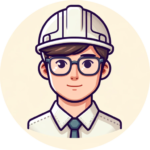
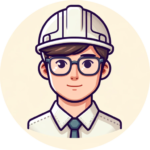
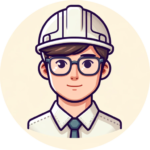
高品質な溶接といえばTig溶接
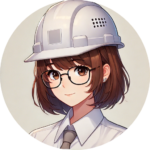
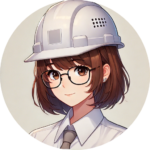
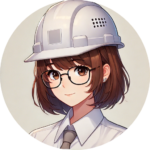
両手をつかうので難しそう
Tig溶接(ティグ溶接)とは、「Tungsten Inert Gas Welding(タングステン不活性ガス溶接)」の略で、タングステン電極を使用し、溶接部を不活性ガスで覆いながら行う溶接方法です。この方法は、空気中の酸素や水分が溶接部に触れるのを防ぎ、金属の酸化を抑えるため、高品質な溶接が可能です。特に、精密さが求められる薄い金属やステンレス鋼、アルミニウムなどの材料に適しており、以下のような特長があります。
- 高品質な溶接が可能:空気の侵入を防ぎ、溶接時の酸化を最小限に抑えるため、非常にきれいで強固な溶接を行うことができます。
- 幅広い金属に対応:ステンレス、アルミニウム、銅、チタンなど、多くの金属に適用できる点が他の溶接方法との大きな違いです。
- 精密なコントロールが可能:手動操作が主流であり、溶加棒を目視で適切に供給しながら溶接を行うため、繊細なコントロールが可能です。
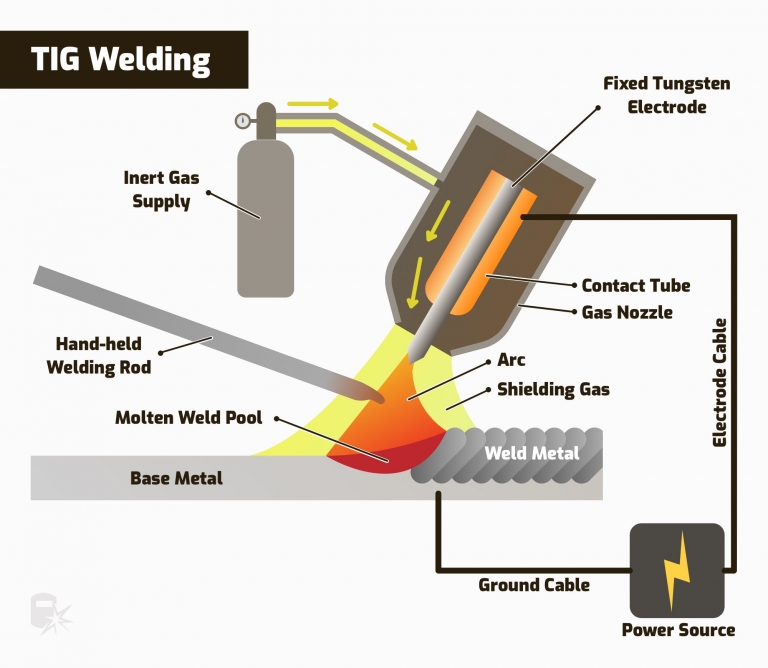
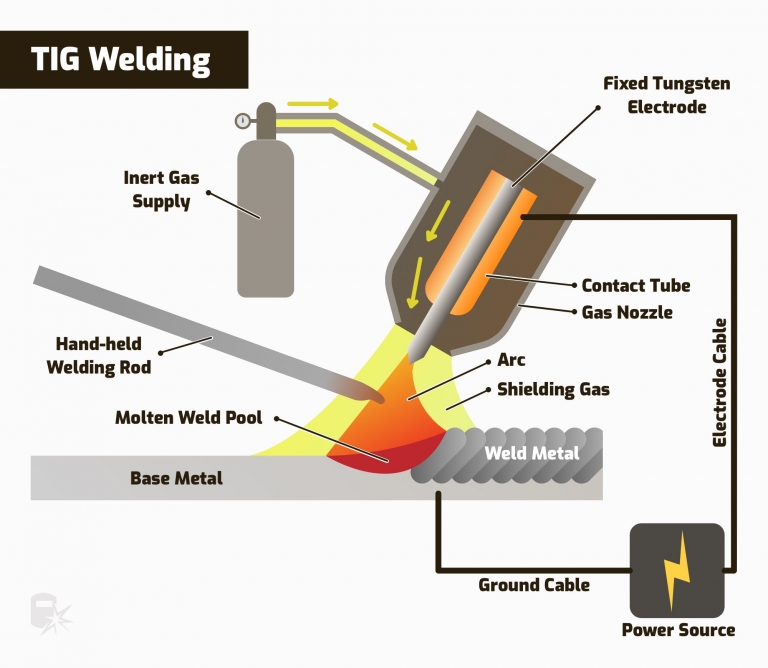
Tig溶接の原理と工程
Tig溶接では、タングステン電極と母材(溶接対象)との間にアークを発生させ、そのアークによって金属を溶かして接合します。この際、不活性ガス(主にアルゴンガス)が電極と溶接部分をシールド(覆う)することで、酸化や不純物の混入を防ぎます。
- タングステン電極:溶接時に溶けない電極で、アークを安定させるために重要な役割を果たします。一般的には、純タングステンやトリウム入りタングステンが使用されます。トリウム入りタングステンは電極の耐久性が高く、再点火性も優れています。
- シールドガス:アルゴンやヘリウムなどの不活性ガスを使用し、溶接部を空気中の酸素や水分から保護します。
Tig溶接の主な応用分野
Tig溶接は、主に以下のような分野で利用されています。
- 航空宇宙産業:高い精度と強度が求められるため、航空機やロケットの部品製作に使用されます。
- 食品・医療機器製造:ステンレス鋼の清浄な溶接面が必要なため、衛生管理が厳しい環境で使用される器具や装置の製造に適しています。
- 自動車産業:排気系や燃料タンクなど、耐久性と美観が求められる部品に多く用いられています。
アルミニウムの溶接について(直流と交流の違い)
Tig溶接では、母材の材質によって使用する電流の種類が異なります。例えば、鉄鋼などの金属では、直流(DC)を使用することが一般的です。これは、直流がアークを安定させ、効率的な溶接ができるためです。
一方、アルミニウムやその合金では交流(AC)を使用します。アルミニウムには酸化膜が形成されやすく、この酸化膜が溶接の障害となるため、交流を使用して酸化膜を破壊する「クリーニング作用」を発生させます。これにより、表面が清浄になり、溶接が可能となります。
Tig溶接の注意点とトラブル防止
Tig溶接は高品質な溶接が可能である一方、いくつかの注意点があります。
- タングステン電極の接触:タングステン電極を母材に直接接触させてしまうと、電極が溶融し、溶接品質が低下します。そのため、高電圧発生装置を使用してアークをスタートさせ、電極の消耗を防ぎます。
- 高周波の影響:Tig溶接では高周波発生装置を使用するため、テレビやラジオなどの近くで作業を行う際は、電波障害が発生する可能性があるため注意が必要です。
Tig溶接の今後
Tig溶接は、その精密さと多用途性から今後も広く利用される技術です。自動化技術との融合も進んでおり、特にステンレス鋼の薄肉管や精密な部品に対して自動溶接技術が導入されています。これにより、溶接の効率化と一貫した品質向上が期待されています。
今後は、より高度な材料や用途に対しても対応できるよう、溶接技術全般の進化とともに、Tig溶接の活用範囲がさらに拡大していくと考えられます。
Tig溶接まとめ
Tig溶接は、その高品質と精密さを必要とする産業において、欠かせない技術です。航空宇宙、自動車、医療機器といった多様な分野で活用されており、特にステンレス鋼やアルミニウムのような酸化しやすい金属に対しても有効です。今後の技術発展とともに、Tig溶接はさらに進化し、多くの産業で重要な役割を果たしていくでしょう。
サブマージアーク溶接とは?―特徴とメリット
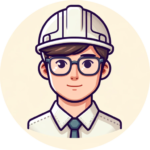
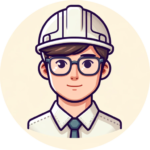
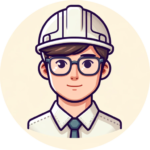
あまり現場ではみない溶接方法のサブマージアーク溶接
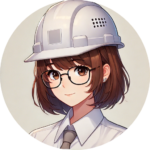
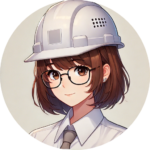
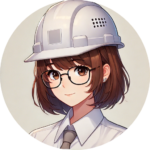
どういうところで使われているのですか?
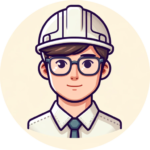
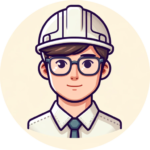
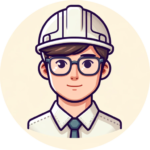
肉厚のタンクの胴板と鏡や胴板どうしの溶接に使われているよ
サブマージアーク溶接(Submerged Arc Welding、SAW)は、厚板の鉄鋼材料を効率的に溶接するために広く使用されている高能率な溶接方法です。この溶接技術は、アークがフラックスという粒状の物質によって覆われる点が特徴です。
この方法により、アーク光やスパッタ(溶接中に飛び散る金属粒子)が外部に出るのを防ぐため、溶接作業が安全かつクリーンに行えるという利点があります。
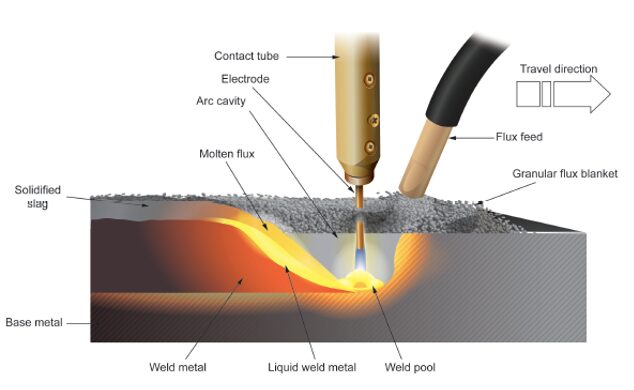
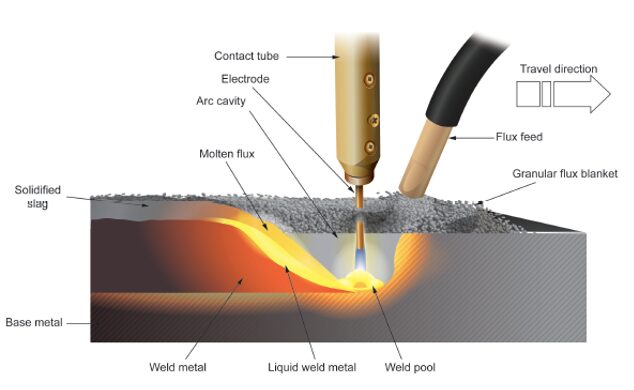
サブマージアーク溶接の基本原理
サブマージアーク溶接は、自動化された溶接方法であり、以下のようなプロセスで進行します。
- 溶接する金属表面にフラックスを散布します。
- ワイヤ(電極)を供給し、母材との間にアークを発生させます。
- フラックスがアークを覆うことで、アーク光やスパッタを外部に漏れさせません。
- 溶融した金属とフラックスが反応し、溶接部が形成されます。
この方法では、高電流(1000Aを超える場合もある)での作業が可能で、溶接部分が比較的平滑に仕上がるため、後の整形作業がほとんど不要となります。また、溶接速度が速く、高い生産性が期待できることから、特に厚板の自動溶接でその効率が発揮されます。
サブマージアーク溶接のメリット
サブマージアーク溶接には、他の溶接方法に比べて多くのメリットがあります。以下にその主要な特徴を挙げます。
1. 高い溶接品質
フラックスによってアークが完全に覆われているため、外部の酸素や窒素と反応するリスクが低く、溶接部の品質が向上します。また、スパッタやヒュームがほとんど発生しないため、作業環境がクリーンである点も優れています。
2. 高い生産性
サブマージアーク溶接は、自動化に適しており、一度に長時間にわたって安定した溶接を行うことができます。これにより、厚板の鉄鋼製品の溶接作業など、大規模なプロジェクトにおいても非常に効率的です。
3. 後処理が少ない
溶接後の表面が比較的滑らかであり、後処理や仕上げ作業がほとんど必要ないため、コスト削減や作業時間の短縮にもつながります。
4. 安全性
フラックスによってアーク光やスパッタが抑えられ、溶接者の安全を確保します。また、溶接中に発生する有害なヒュームも少ないため、作業環境への悪影響が軽減されます。
サブマージアーク溶接の応用分野
サブマージアーク溶接は、その高効率性と自動化への適合性から、以下のような分野で幅広く活用されています。
- 造船業:船体の大型構造物の溶接に最適です。
- 建設業:鋼構造物や橋梁の溶接作業に広く用いられています。
- 石油・ガス産業:パイプラインやタンクの溶接にも使用されることが多いです。
- 重機・大型機械の製造:高強度の材料を使用するため、サブマージアーク溶接の高品質な溶接が求められます。
サブマージアーク溶接の課題と対策
一方で、サブマージアーク溶接にもいくつかの課題があります。その一つは、装置の初期導入コストが高い点です。しかし、長期的な生産性の向上や品質の安定を考慮すれば、コストパフォーマンスは高いと言えます。また、溶接速度が速いことから、適切な操作技術や監視が必要となる場合もあります。
まとめ
サブマージアーク溶接は、高電流を使用して安定した溶接を行い、スパッタやヒュームを抑えることで作業環境を保護しながら、高品質な溶接が可能な技術です。特に厚板の鉄鋼製品の溶接や、建設・造船業などでの大規模なプロジェクトにおいて、その効率性は非常に大きなメリットとなります。初期導入コストや技術的な要件をクリアすれば、企業にとっては長期的に価値のある投資となるでしょう。
ガスシールドアーク溶接(MIG/MAG溶接)
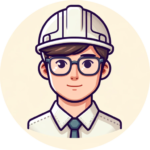
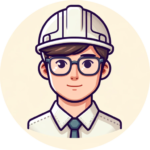
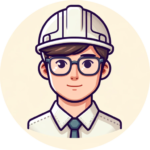
半自動溶接とも呼ばれる溶接方法だね
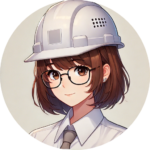
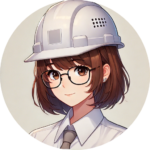
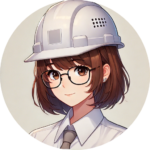
Tigと違ってワイヤーが自動供給されるので便利ですね
ガスシールドアーク溶接(Gas Shielded Metal Arc Welding)は、主にMIG(Metal Inert Gas)溶接とMAG(Metal Active Gas)溶接として知られる技術で、現代の製造業で広く使用されています。この溶接技術は、溶接アークおよび溶接金属をシールドガスで覆うことで、大気から保護しながら高品質な溶接を実現するものです。
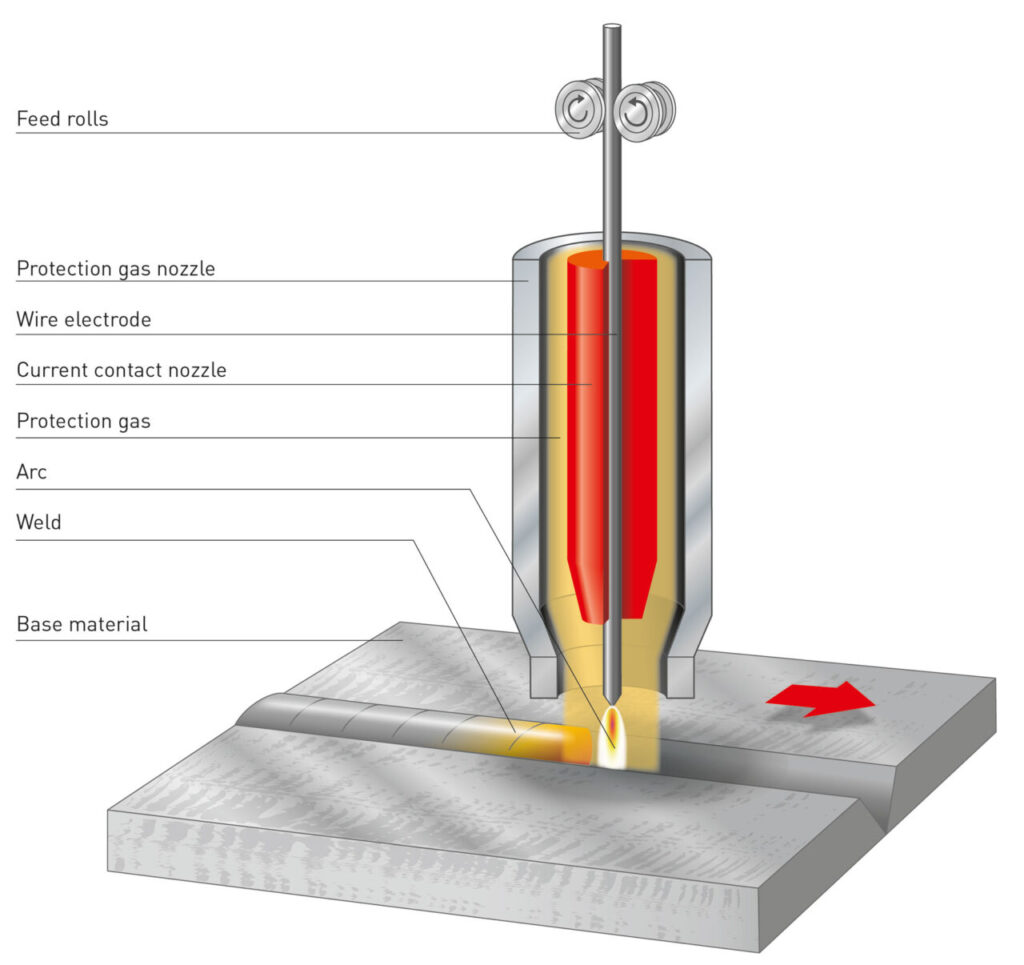
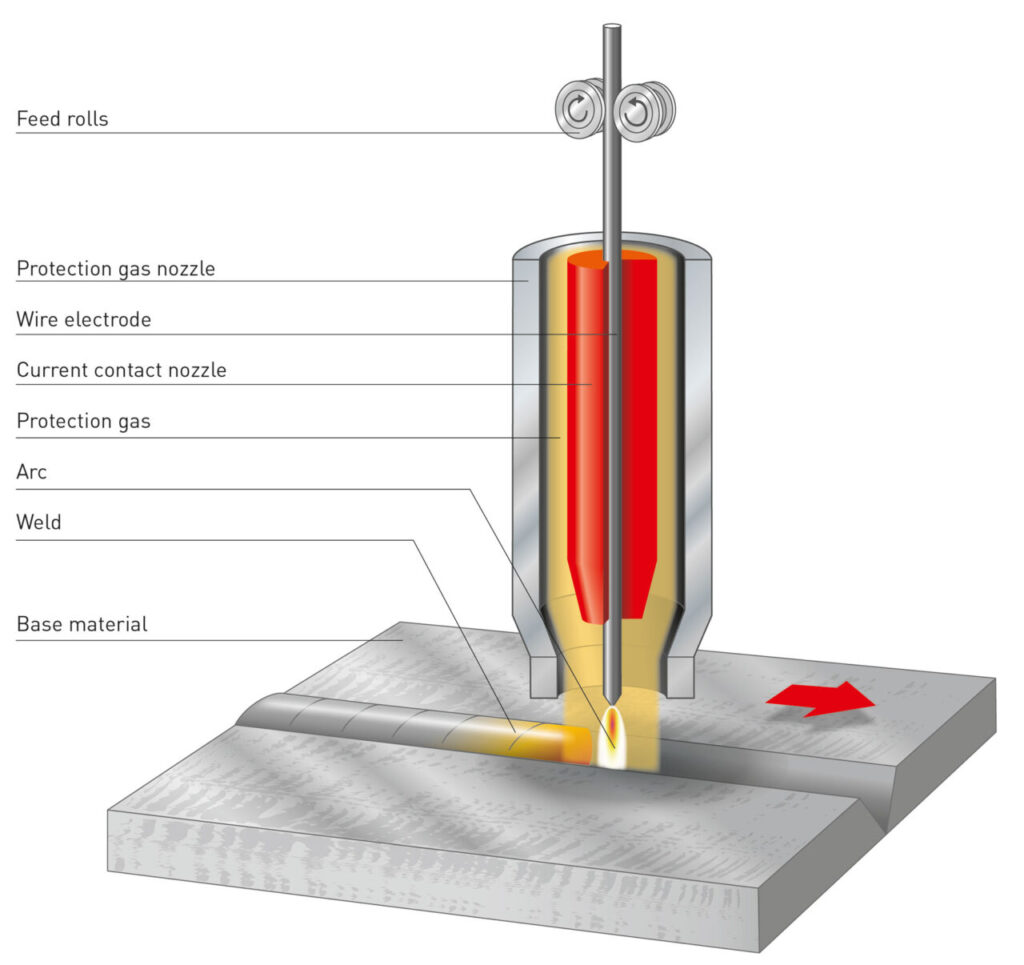
ガスシールドアーク溶接の基本原理
ガスシールドアーク溶接では、自動的に供給されるワイヤ(電極)と母材との間にアークを発生させます。このアークによってワイヤが溶融し、溶接部が形成されます。ここで、溶接アークや溶融金属は、シールドガスと呼ばれるガスによって外部の大気から保護されます。シールドガスの役割は、酸素や窒素などの大気成分が溶接部に混入することを防ぐことで、溶接品質の向上に寄与します。
MIG溶接とMAG溶接の違い
- MIG溶接(Metal Inert Gas Welding)は、不活性ガス(例:アルゴン)をシールドガスとして使用します。アルゴンのような不活性ガスは、溶接金属と化学反応を起こさないため、主にアルミニウムやステンレス鋼などの溶接に適しています。
- MAG溶接(Metal Active Gas Welding)は、活性ガス(例:炭酸ガス、またはアルゴンと炭酸ガスの混合ガス)を使用します。炭酸ガスは酸化作用を持つため、主に鉄鋼の溶接に適しており、スパッタの低減を目的としています。
ガスシールドアーク溶接のメリット
この溶接方法には、多くのメリットがあり、現代の製造業で広く採用されています。
1. 高品質な溶接が可能
シールドガスによってアークが安定し外部の空気から保護されるため、酸素や窒素の混入が防止され、溶接品質が高まります。特にMIG溶接では、アルミニウムやステンレス鋼のような腐食に弱い材料にも適しています。
2. 自動化に適している
ガスシールド消耗電極式アーク溶接は、自動溶接や半自動溶接に適しており、大規模な生産ラインで使用するのに非常に便利です。ワイヤの自動供給によって、長時間にわたる安定した溶接が可能です。
3. スパッタが少ない
特にMAG溶接では、シールドガスの組成を適切に選ぶことで、スパッタの発生を最小限に抑えることができ、後処理の手間が減ります。
MIG溶接とMAG溶接の具体的な適用分野
1. MIG溶接の適用分野
MIG溶接は、主にアルミニウムやステンレス鋼など、腐食しやすい材料の溶接に使用されます。不活性ガスであるアルゴンを使用するため、これらの材料に対する高品質な溶接が実現します。
- アルミニウムの溶接:一般的にアルゴンが使用されますが、厚板の溶接ではアルゴンとヘリウムの混合ガスが使用されることもあります。ヘリウムを加えることで、溶込みが改善されます。
- ステンレス鋼の溶接:ステンレスのアークを安定させるために、アルゴンに酸素を2%程度混合したガスが使用されることが多いです。
2. MAG溶接の適用分野
MAG溶接は、鉄鋼材料の溶接に適しています。スパッタの発生を抑えながら、高効率での溶接が可能です。
- 鉄鋼の溶接:シールドガスとして炭酸ガスが主に使用されます。多くの場合、アルゴンと炭酸ガスを混合したガス(アルゴン80%、炭酸ガス20%)が最適とされます。
- 建設や重機産業:鉄鋼の高強度構造物の製造に使用され、橋梁や建物のフレーム、重機の製造に適しています。
ガスシールドアーク溶接の課題と対策
ガスシールド消耗電極式アーク溶接には多くの利点があるものの、課題も存在します。その一つは、シールドガスが外部の風などの影響を受けやすいことです。屋外での使用には、風防などの対策が必要になります。
また、適切なシールドガスの選定が必要であり、溶接する材料や用途に応じて最適なガスを選ぶことが品質を左右します。
さらに、装置の初期導入コストや操作技術も課題となる場合がありますが、高効率な溶接作業と優れた品質管理を実現するための重要な要素であることを考慮すれば、長期的には大きなメリットが得られます。
ガスシールドアーク溶接まとめ
ガスシールド消耗電極式アーク溶接は、MIG溶接とMAG溶接を総称した溶接技術であり、主に鉄鋼、アルミニウム、ステンレス鋼の溶接に広く利用されています。シールドガスによる大気からの保護と、自動供給されるワイヤによって安定したアークが得られることが特徴です。用途に応じて適切なシールドガスやワイヤを選定することで、高品質な溶接を効率的に行うことができます。
プラズマアーク溶接
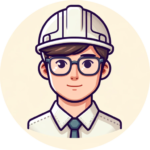
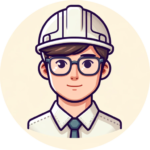
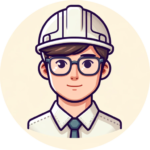
あまり一般的ではないかな?
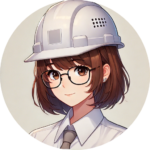
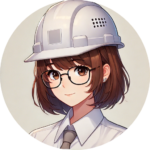
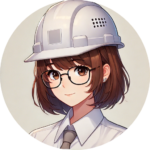
確かにあまり聞いたことがないかも
プラズマアーク溶接(Plasma Arc Welding、PAW)は、ティグ溶接(TIG溶接)と同様の基本原理を持ちながらも、アークの特性をより効果的に利用することで、非常に高温での溶接が可能な高度な技術です。この溶接法では、アークの温度が2万~5万度に達し、ステンレス鋼や特殊な金属の精密な溶接が求められる場合に使用されます。
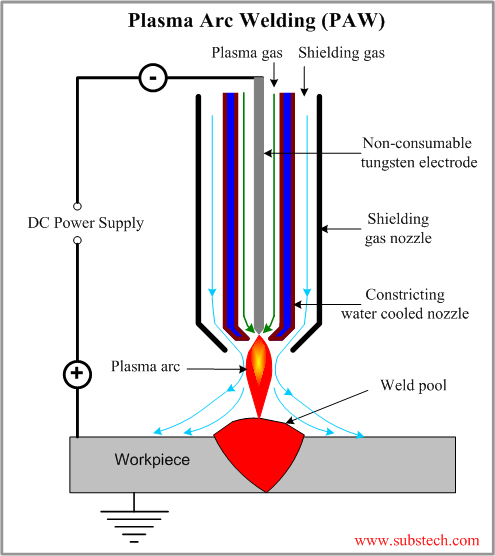
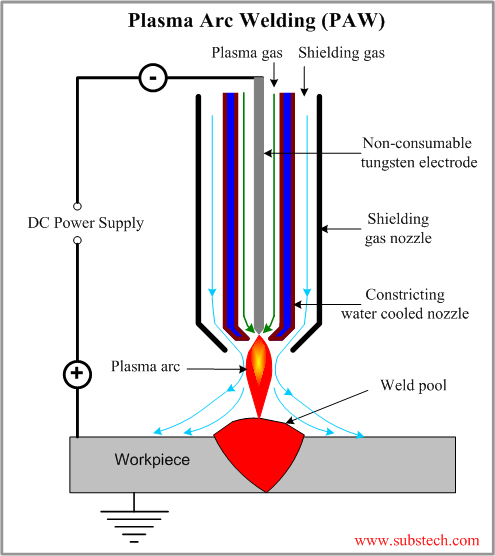
プラズマアーク溶接の基本原理
プラズマアーク溶接は、ティグ溶接と同じく非消耗性のタングステン電極を使用します。しかし、PAWは特に熱的ピンチ効果を活用しています。アーク周囲を冷却することで、アーク中心部の温度をより高温にする現象が起こり、溶接部に集中して高エネルギーが供給されます。この高エネルギーを利用して、非常に精密な溶接が可能となります。
また、プラズマアーク溶接には以下の二つのモードがあります。
- マイクロプラズマモード:低電流での微細な溶接に使用され、薄板や細かい部分の溶接に適しています。
- キーホールモード:アークが材料を貫通し、裏側まで届くほどの高温になるため、片側からの溶接で十分な貫通が得られます。これにより、開先加工を最小限に抑えることができ、厚板でも一パスで溶接できるため、非常に効率的です。
プラズマアーク溶接の特徴
プラズマアーク溶接には、他の溶接方法にはない独自の特徴がいくつかあります。
1. 高温度での溶接が可能
アークの温度が2万~5万度に達するため、厚い金属材料でも一度に深い溶接を行うことができます。これにより、複数回の溶接を必要とせず、高効率な作業が可能です。
2. 熱的ピンチ効果
アークを冷却することで中心部分の温度を極限まで高め、溶接箇所に集中させることができます。この熱集中により、より正確かつ精密な溶接が行えます。
3. 高い寸法精度
プラズマアーク溶接では、溶接部の寸法精度が極めて高いため、ステンレス鋼などの精密な作業に適しています。このため、自動化された溶接プロセスに広く利用されており、特に製品の寸法精度が厳しく要求される業界で重宝されています。
4. キーホール溶接
プラズマアーク溶接のキーホールモードでは、アークが金属を貫通し、穴が開いたような状態を作り出して溶接を行います。この方法では、片側からの溶接で強固な結合を得ることができ、従来の方法よりも効率的に作業を進めることができます。
プラズマアーク溶接のメリット
プラズマアーク溶接には、以下のような多くのメリットがあります。
- 高温での作業が可能なため、厚い材料でも効率的に溶接できる。
- 寸法精度が高いため、精密な部品やステンレス鋼の溶接に最適。
- 自動化が容易であるため、産業ロボットを使用した生産ラインでの利用が可能。
- キーホール技術を使用することで、片側からの溶接でも高品質な仕上がりを実現。
プラズマアーク溶接のデメリット
一方で、プラズマアーク溶接にはいくつかのデメリットも存在します。
- 機器や装置が高価であり、初期導入コストが高い。
- 特殊な操作技術が必要であり、熟練した技術者が求められる。
- 複雑な冷却システムや高精度な設定が必要で、メンテナンスや運用コストがかかる。
プラズマアーク溶接の応用分野
プラズマアーク溶接は、その高温・高精度な特性から、特定の分野で広く使用されています。特に以下の分野でその効果が発揮されます。
- 航空宇宙産業:ステンレス鋼や耐熱合金など、高温に耐える素材を使用するため、精密で高温の溶接が必要です。
- 半導体製造装置:寸法精度が厳しく求められる装置の部品溶接に適しています。
- 医療機器:精密な溶接が求められるため、プラズマアーク溶接の高精度が役立ちます。
プラズマアーク溶接まとめ
プラズマアーク溶接は、ティグ溶接と同じ原理を活用しつつ、熱的ピンチ効果による高温度での作業が可能な高度な溶接技術です。特に、ステンレス鋼や高精度な部品が必要とされる分野での応用が進んでいます。導入コストや技術者の習熟度が課題ではありますが、精密さと効率性を重視する業界において、その価値は非常に高いです。技術の進化に伴い、さらなる利用拡大が期待されるでしょう。
まとめ
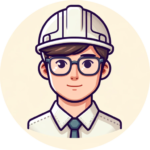
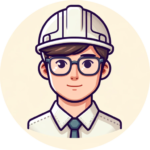
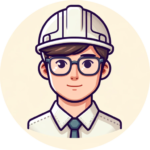
ということで溶接の基本をまとめたよ
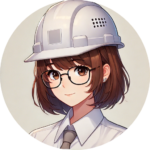
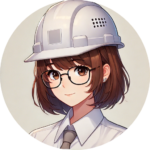
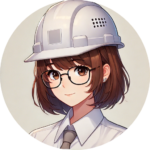
色々な溶接方法があるんですね。覚えておかないと迷いそう
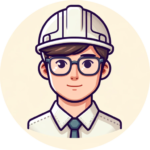
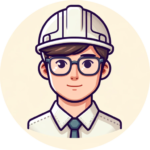
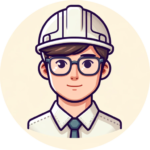
そうだね。適材適所で使い分けるし、開先設計とかも気をつける必要がある。開先についてはまた別の機会に話そう。
溶接施工は、建築や製造業をはじめ、多くの産業分野で欠かせない技術です。この記事では、溶接の基本概念と主な溶接方法について解説しました。
溶接には3つの主要な方法があります。まず、「融接法」は接合部分を高温で溶かし、一体化させる方法です。特にアーク溶接が代表的で、建築や圧力容器の製造に広く使用されます。融接法では、熱影響部(HAZ)の管理が溶接の品質に大きな影響を与えるため、慎重な技術が求められます。
次に、「圧接法」は熱と圧力を加えて接合する方法です。スポット溶接やシーム溶接などが代表的で、異なる金属の接合に適しています。特に、異種金属同士の接合が必要な場面では、圧接法が優れた結果をもたらします。
「ろう付け」は、母材よりも低い融点の金属を使って接合する方法で、細かい部品や複雑な構造に向いています。硬ろう付けと軟ろう付けがあり、用途によって使い分けられます。
溶接の基本技術とその特徴、利点、そして安全対策につい理解をして、各技術の違いを理解することで、適切な方法を選択できるようになります。
コメント