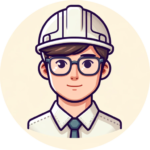
プラント機器の信頼性と安全性を確保するために非破壊検査は必須だよ
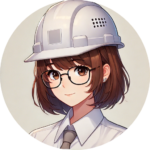
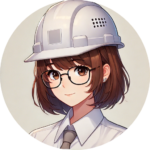
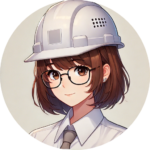
具体的にはどう言うところに使われるんですか?
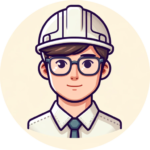
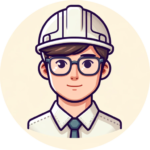
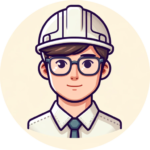
まず製作物としては配管やタンクの溶接部だね。溶接は特に不具合が発生しやすい
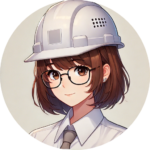
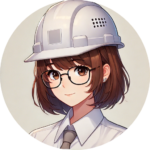
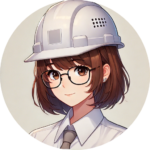
つまり溶接部だけをやっておけば良いと
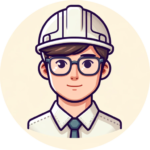
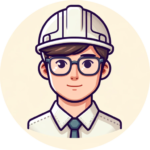
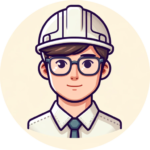
溶接部以外にも例えば疲労でクラックが入った場合どこまでクラックがあるか?タービンにクラックがないかの定期検査など応用範囲は広いよ
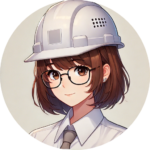
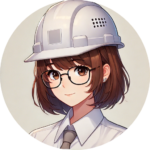
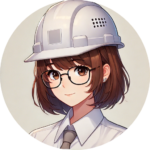
製作時の品質チェックだけでなく、設備保全にも重要と言うことですね!
プラント機器や機械において、信頼性と安全性を確保することは最優先事項です。これらの設備は、高圧・高温環境や大きな力が加わる過酷な条件下で使用されるため、時間の経過とともに金属疲労や腐食、亀裂、欠陥などが発生する可能性があります。これらの問題が進行すると、最悪の場合、機器の故障やプラント全体の停止、さらには人的・環境的な被害に繋がる可能性もあります。
非破壊検査(Nondestructive Testing: NDT)は、設備や部品を破壊せずに内部および表面の欠陥を検出する技術です。これにより、製作した機器や運用中の機器をそのまま検査できるため、設備の停止時間を最小限に抑えつつ、早期に問題を発見して対処することが可能です。また、非破壊検査は定期点検やメンテナンスの一環として利用されるだけでなく、新規設置時の品質確認や製造過程における検査としても重要な役割を果たします。
非破壊検査を適切に行うことで、次のようなメリットが得られます:
- 安全性の向上: 事故や故障を未然に防ぐことで、作業者や周囲環境の安全を守る。
- コスト削減: 重大な故障を回避することで、修理や交換にかかるコストを削減できる。
- 信頼性の向上: 機器やプラント全体の運用信頼性を高め、生産性を向上させる。
これらの理由から、非破壊検査はプラント機器や機械において不可欠な技術であり、定期的かつ適切に実施することが求められています。
非破壊検査の主要な方法
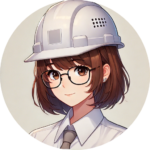
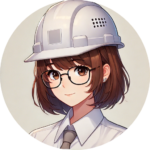
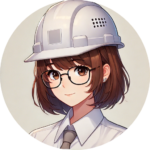
非破壊って言うと壊さない検査なのでいろいろありますよね?
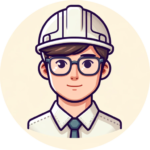
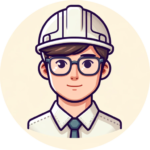
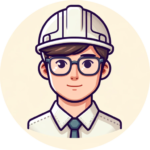
そうだね、ノギスや外観検査も非破壊検査っていう。だけど今回は破壊につながる欠陥がないかの検査に限定しているよ
非破壊検査の方法は非常に多くあります。例えばノギスで寸法が適切かどうかを測定するのも非破壊検査の一つです。ひずみゲージでひずみや残留応力を測定することもそのうちの一つです。
しかし、一般的に非破壊検査というとプラント機器製作の際や、定期検査において割れなどの欠陥がないか検査する方法を言うことが多いです。
この場合の主要な方法としては、浸透探傷試験(PT:penetrant testing)、磁粉探傷試験(MT:magneticparticle testing)、放射線透過試験(RT:radiographic testing)、超音波探傷試験(UT : ultrasonitesting)、過流探傷試験(ET:eddcurrent testing)などがあります。
他にも何種類かあるのですが、今回はこれらの非破壊試験の概要について解説します。
浸透探傷試験
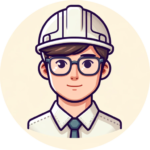
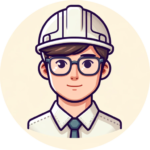
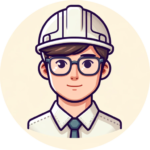
まず最も基本的な浸透探傷試験
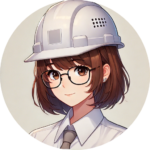
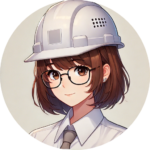
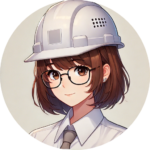
あの赤い液で染めるやつですね!
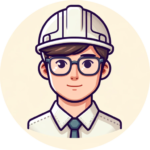
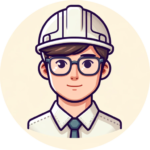
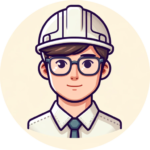
赤い色以外にもあるんだよあれは。最後の現像工程で見えやすい色を使うべきだね
概要
浸透探傷試験は、金属の表面に現れた傷を見つける非破壊検査法です。被試験体表面に塗られた浸透液(赤い染色浸透液または黄緑色の蛍光浸透液)は表面に傷が出ていると、その内部に浸透します。
表面の液を拭い去ったあと、白い粉末を散布すると、傷内部に浸み込んでいた浸透液が粉によって吸い出され、傷の拡大された指示模様が現れます。この検査法では、傷が表面に開口している必要があります。
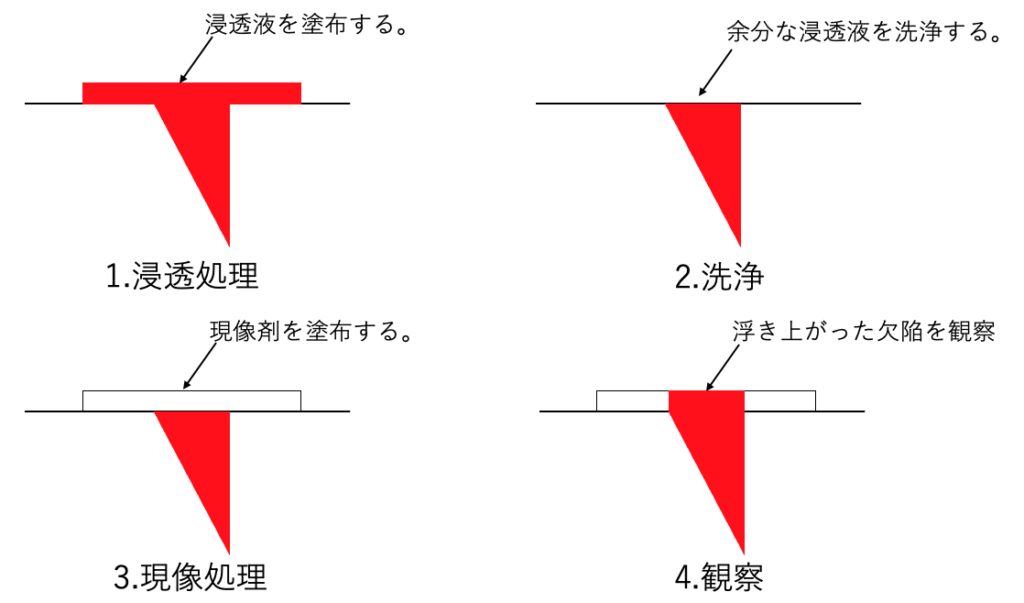
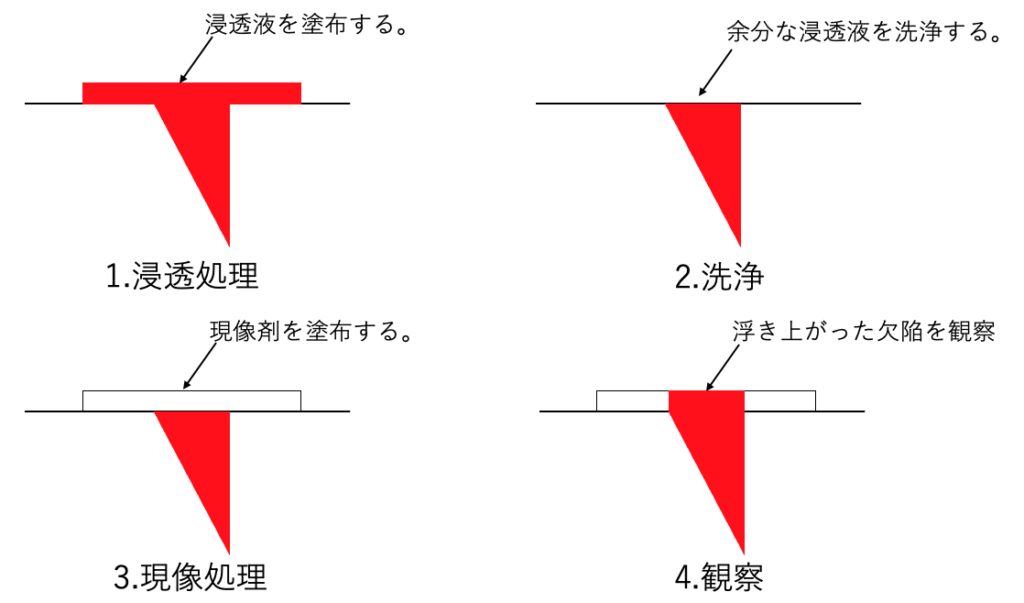
利点
- 簡単でコストが低い: 特別な機材が不要で、操作が比較的容易なため、現場でも手軽に実施できる。
- 複雑な形状の部品にも適用可能: 試験体の形状に制約が少ないため、複雑な形状の部品や構造物にも対応可能。
- 非常に小さな表面の欠陥も検出可能::マイクロメートル単位の微細な表面欠陥でも検出が可能で、視覚的に確認できる。
- 多様な材料に適用できる:金属だけでなく、ガラス、プラスチック、セラミックにも適用できる。
欠点
- 内部の欠陥は検出できない: 表面に開口していない欠陥や、内部に存在する欠陥は検出が不可能。
使用用途
- 溶接部や鋳物の表面欠陥の検出: 溶接部や鋳造部品の表面に開口したクラックやピットの検出に適している。
- 航空機や自動車部品の定期検査: 疲労破壊の早期検出に用いられ、メンテナンスの重要な一環として位置付けられる。
磁粉探傷試験
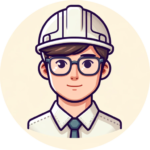
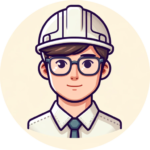
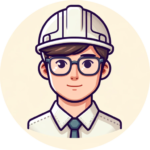
次は磁粉探傷試験。そのあの通り磁粉を使うので磁性体以外は使えない
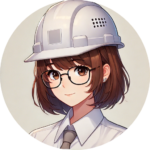
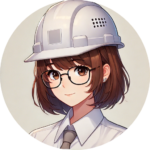
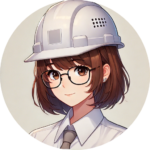
結構限定されそうですけど何がいいんですか?
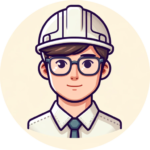
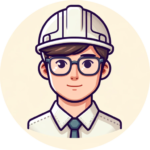
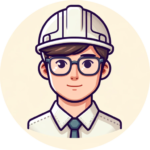
表面に近いクラックは高精度で検出できるので浸透探傷試験よりも欠陥を発見しやすいよ
概要
磁粉探傷試験は、表面または表面に近い傷を見つけるのに有効な非破壊検査法です。
磁性体(金属)が磁化すると、磁束が生じます。この磁束は被試験体の表面およびその直下に存在する傷により漏れ出すため、漏えい磁束が形成されます。
被検査面に磁粉(鉄粉など)を撒くと、漏えい磁束により傷部に集中的に吸着され、傷の指示模様が現れます。
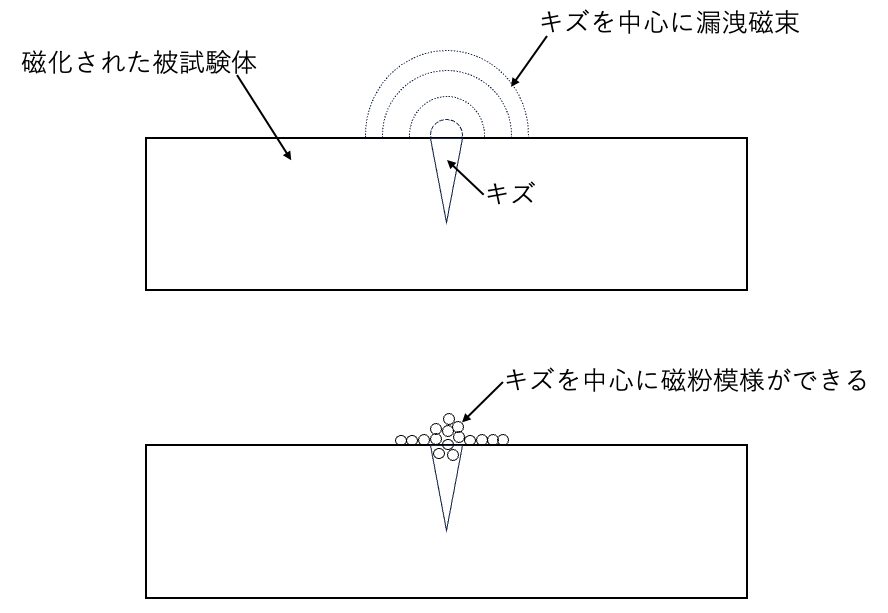
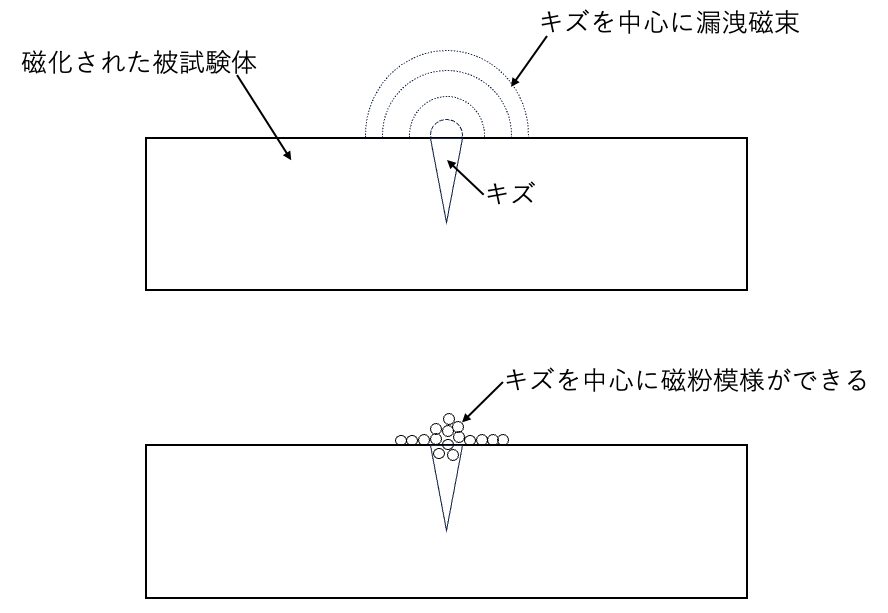
利点
• 表面および表面近くの傷を高精度に検出可能: 特に表面に非常に近い内部欠陥を検出するのに優れており、感度も高い。
• 迅速な検査が可能: 結果が即時に得られる。
欠点
- 磁性材料に限定される: 磁化が必要なため、鉄やニッケルなどの磁性材料以外には適用できない。特にオーステナイト系ステンレス鋼には使用できないので注意。
- 検出可能な傷の深さは限られている: 表面に近い欠陥には強いが、深さがある欠陥の検出は難しい。
- 環境に影響を受けやすい: 表面の清浄度や磁粉の選択により、検査結果が変わる可能性がある。
使用用途
- 鉄鋼構造物や車両部品の定期点検: 橋梁や建物の鉄骨部品、車両のシャーシや車軸などの疲労クラック検出に利用される。
- パイプラインやボイラーの溶接部検査: パイプラインや圧力容器の製造・保守の際に使用され、信頼性の高い検査方法として広く採用されている。
放射線透過試験
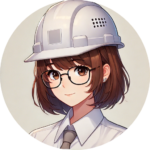
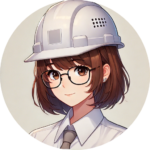
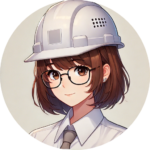
放射線と聞くと危険そうですね
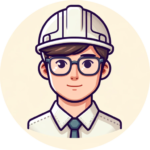
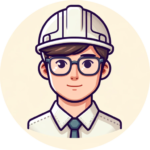
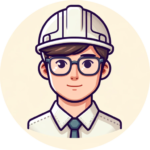
実際に行う時は人払いの徹底など安全対策は必須。ただ内部欠陥を検出するには非常に有効。さら圧力容器の溶接部は放射線透過試験によって強度が決まるのでよく理解しておこうね
概要
放射線透過試験は、溶接部や鋳物の内部欠陥を調べる非破壊検査法の1つです。検査は放射線が被試験体を通過する時、その厚さに応じて指数的に減衰する原理を利用します。
主にX線やガンマ線が使用され、透過した放射線をフィルムに受け、その感光度合いにより欠陥を評価します。
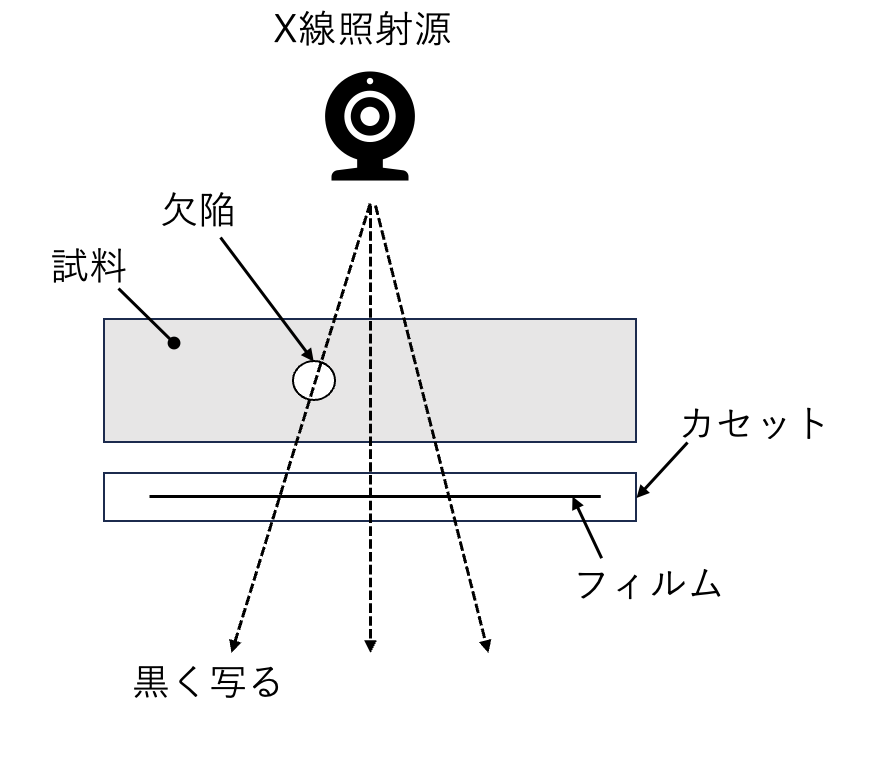
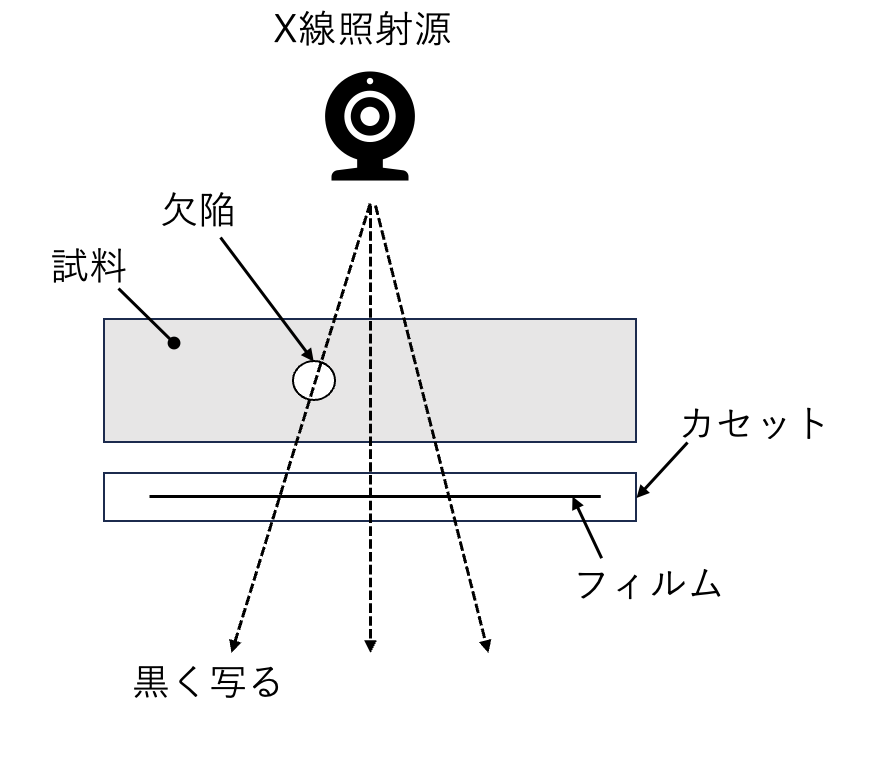
利点
- 内部の欠陥を直接観察できる: 試験体の内部構造を視覚的に確認でき、欠陥の位置や形状を詳細に特定可能。
- 広範囲の欠陥検出が可能: 小さなボイドから大きなクラックまで、さまざまな種類の欠陥を検出可能。
- 材料の厚さに左右されにくい: 厚い材料でも適用可能で、構造体の一部や厚さの異なる部分も均一に検査できる。
欠点
- コストが高い: 専用の放射線源やフィルム現像設備が必要で、運用コストも高い。
- 放射線被曝のリスクがある: 検査作業者は放射線防護を徹底する必要があり、作業環境に制限がある。
- 内部構造物の重なりに弱い: 複数の欠陥が重なると、検出が難しくなる場合がある。また、放射線入線方向に直角な面にある微細欠陥、表面的に広がりのある欠陥には不向き。
使用用途
- 配管や圧力容器の溶接部検査: 配管や圧力容器などの溶接部における内部欠陥(溶接不良、ボイドなど)の検出に使用される。特に圧力容器の溶接部は、放射線透過試験を何%行うかによって、強度計算が変化するので注意する。
超音波探傷試験
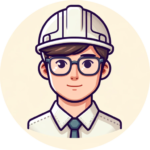
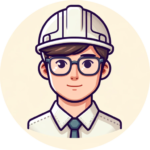
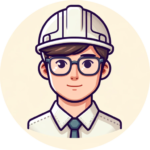
放射線よりは安全な試験だね
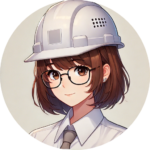
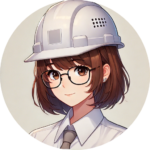
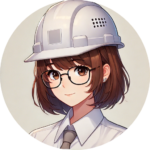
じゃあなんでこっちを幅広く使わないんですか?
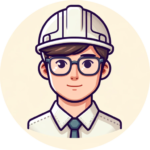
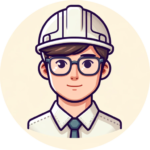
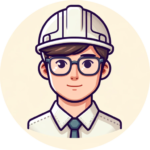
放射線透過試験は写真のように視覚的に確認できるけどこちらは波形。なのでその診断に技術が必要なんだ
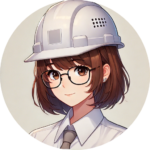
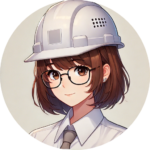
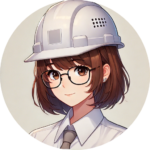
試験を行って判断するにも技術がいるってことですね!
概要
超音波探傷試験は、金属の内部欠陥を調べる非破壊検査法の1つです。超音波は気体、液体、固体の中を伝播し、直進性があり、異なる材料との境で反射する性質を利用して、傷の所在を突き止めます。
被試験体表面から超音波パルスを内部に送り、内部の傷から反射される超音波(エコー)を検出し、その大きさと戻ってくるまでの時間から傷の大きさと距離を知ることができます。
利点
- 内部の欠陥を非破壊で検出可能: 放射線を使用せずに内部の詳細な検査が可能で、安全かつ効果的。
- 検査結果をリアルタイムで得られる: エコーを即座に解析できるため、その場で欠陥の有無を判断できる。
- 表面仕上げや材料に依存しにくい: 表面が荒れていても高精度で検査でき、多様な材料に適用可能。
欠点
- 形状や材質によっては検出が難しい場合がある: 複雑な形状や異材接合部では、超音波の伝播が乱れることがある。
- 厚みや形状に制約がある: 厚い部材では音波の減衰が増すため、検出感度が低下することがある。
- 専門技術が必要: 検査結果の解釈には高度な技術が要求され、熟練した検査技術者が必要。
使用用途
- 鉄道レールや車軸の検査: 鉄道車両のレールや車軸に発生する内部亀裂の検出に広く利用されている。
- 鋼構造物の定期点検: 橋梁やビルの鋼材など、大型構造物の内部欠陥の検出に適用される。
渦流探傷試験
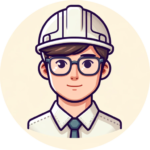
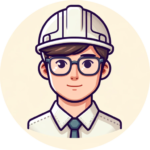
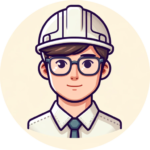
こちらは電流の変化を検出する試験方法だね。
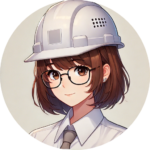
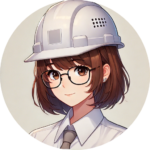
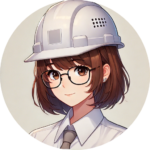
これも超音波同様検査に技術がいるんですね
概要
渦流探傷試験は、鉄鋼や非鉄金属などの導電性材料の表面および表面近くの傷を検出する非破壊検査法です。
被試験体にコイルを近づけ、コイルに交流電流を流すと、電磁誘導により試験体の表面に渦電流が発生します。傷があると渦電流の流れが変わり、その結果コイルの電流も変化します。この変化を検出することで、傷の存在を確認します。
利点
- 表面および表面直下の欠陥を高精度で検出可能: 特に微細な傷や腐食の検出に優れ、高感度の検査が可能。
- 非接触での検査が可能: 渦流探傷試験は非接触で実施できるため、検査対象物にダメージを与えずに検査が行える。
- 迅速な検査と自動化に適している: 結果が即座に得られるため、大量生産ラインでの自動化検査に適している。
欠点
- 材質に依存する: 渦流探傷は導電性材料に限定されており、非導電性材料には使用できない。
- 複雑な形状には適用しにくい: 検査対象物の形状や表面状態が複雑な場合、結果の解釈が難しくなる。
- 深部の欠陥検出は困難: 表面近くの欠陥には敏感だが、深部の欠陥の検出能力は限られる。
使用用途
- 航空機のアルミ部品やタイタニウム部品の検査: 軽量で強度のあるアルミやタイタニウムの部品に使用され、微細な表面傷の検出に用いられる。
- パイプラインやボイラーの定期検査: 鋼管やボイラーの腐食や亀裂を検出し、保守や修理に活用される。
実際の運用
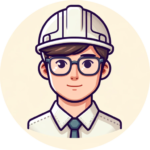
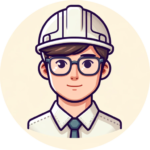
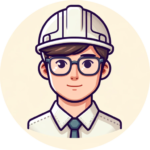
実際にはどれか単体で使用するということは少なく、複数合わせて使用するよ
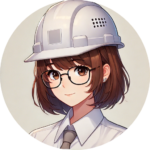
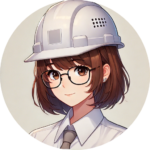
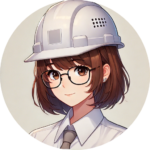
じゃあ検査員は複数の検査方法を理解していないとダメってことですか?
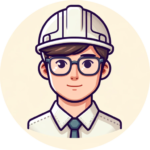
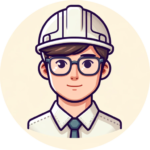
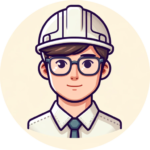
そうだね。あと重要なのはさっきも言った通り溶接部の強度は放射線透過試験により変化するので、設計時に決定して検査員に指示する必要があるよ
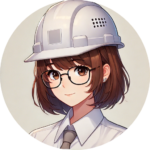
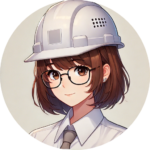
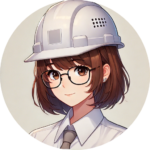
設計する時も非破壊検査をしっかり理解しないとダメってことですね!
とは言ってもこれら非破壊検査単独で使用するかと言うとそうでもない時があります。例えば溶接部の検査の場合は表面の欠陥と内部の欠陥の両方を検査する必要があります。
また、圧力容器の溶接継ぎ手は放射線透過試験により溶接効率が変わるので、設計上行わなければいけない(この表現は少しおかしいですが)場合もあります。
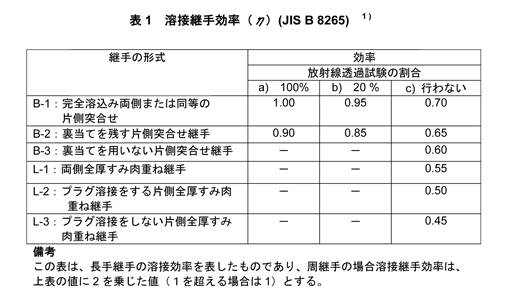
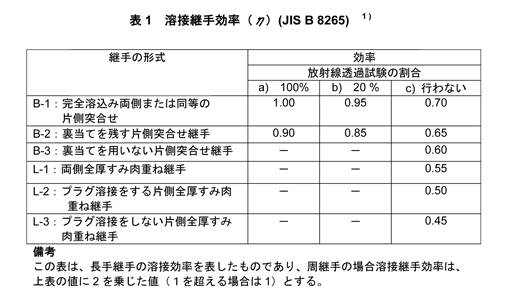
と言うことで実際の運用としては
溶接部:浸透探傷試験で表面の割れなどを検査。必要であれば放射線透過試験で内部欠陥の検査
曲げ部の割れ:浸透探傷試験、磁粉探傷試験で検査
鋳物の内部欠陥(巣):放射線透過試験で検査
各種機器の定期検査:対象により浸透探傷試験で表面欠陥の検査。定期検査の場合は放射線透過試験が難しいので超音波探傷試験や渦流探傷試験で内部血管の検査
と言う感じになります。特に放射線透過試験に関しては準備が必要なことと、放射線を取り扱うので周囲に人が存在しない状態での試験が必要です。
そのため、定期点検の時などはあまり使えず、それ以外の検査方法で内部欠陥の検査が必要です。
非破壊検査はプラント機器、機械設備には必須
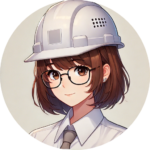
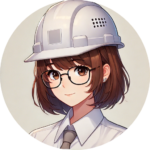
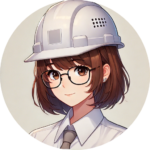
非破壊検査の種類と概要が理解できました。検査員に任せっきりにせず設計側も理解しないとダメなんですね
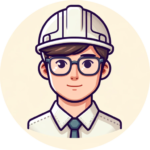
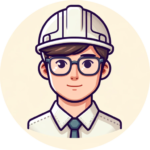
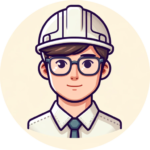
プラント全体の品質に関わるからね。検査員任せにせずしっかりと理解して設計しよう。
このように、非破壊検査はプラント機器や機械の信頼性と安全性を確保するために欠かせない技術です。さまざまな検査方法を駆使して、表面および内部の欠陥を効率的に検出し、適切なメンテナンスや修理を行うことで、事故やトラブルを未然に防ぐことができます。
しかし、検査方法によっては欠陥の検出に不適な場合があります。どのような材料で、どのような部位で、どのような欠陥を検出(検査)したいのか?それにより適切な検査方法は変わります。
適切な非破壊検査によりプラント機器、機械を安全に製作し長期間使用できるようにしましょう。
コメント