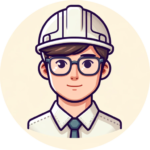
プラントや工場の稼働を開始してから、いや稼働前から始まるもので最も長いのはなんだと思う?
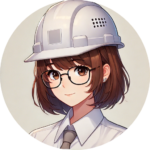
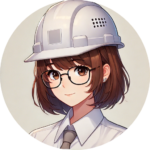
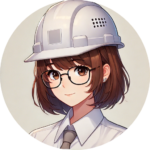
え〜なんでしょう?あ!生産計画とか!
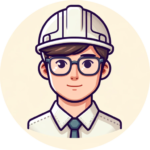
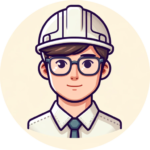
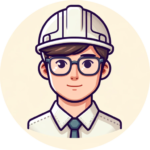
答えは保全だね。プラントや工場の稼働前から適切な計画が必要だし、稼働している限りはずっと必要
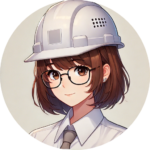
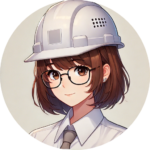
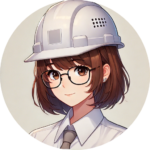
事後保全、予知保全、計画保全、TPMとかいうやつですね
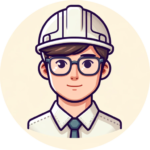
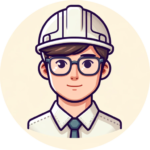
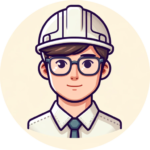
よく知っているね!でも言葉だけ知っていてもうまく運用できるとは限らないから解説していこう!
プラントや工場を建設して試運転して立ち上げて、「よし!生産開始!」となって生産が始まりますが(そんなに簡単ではないですが)、建設までに要する期間よりも長い活動があります。
それが設備保全です。プラントや工場の運用と共に設備の保全は欠かせませんし、将来的にその工場やプラントが完全に定するまで続く最も長い活動です。
そして今やその設備保全といえば「事後保全」や「予知保全」そして「TPM」などいろいろとかっこいいい用語やトレンドがありますが、設備保全活動を有効に活動させるためにはそもそもの「設備保全」の正確な知識が必要です。
そこで今回は設備保全活動を行なっていく上で必要な”超”基礎知識を解説していきます。
TPMの前に設備保全とは何か?学んでほしい!
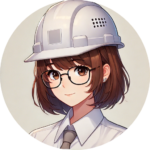
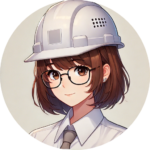
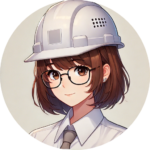
みんなでTPMをすればいいんじゃないですか?
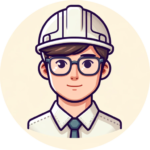
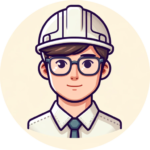
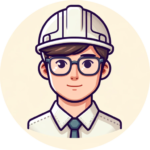
TPMは全員で行う保全活動だけどその前に全員が設備保全を学ぶ必要があるね。
巷ではプラントや工場の設備保全といえばTPMと呼ばれる、全員参加の設備保全の導入が盛んです。これは今までは「私作る人」「私直す人」となっていた工場の設備だけでなくロス削減の活動全員で行うことで、工場のロスを極限まで削減するという活動です。
設備保全もこの中に入り、例えば強制劣化対策のための清掃や日常点検表などの見直しも含まれます。しかし、非常にありがちなのが「保全とは何か」という考えがそもそも曖昧なままで活動を始めて、とりあえずTPMの仕組みを作ったことに満足してしまうことです。
こうなってしまうと本質的な設備保全、つまり「安全を第一として少しでも製造原価の低減を目指す活動」が疎かになり、TPMのルールにもとづいて活動することが中心となってしまいます。
そのようなことを避けるためにはまず設備保全を担当するメンバーだけでなく、生産に関わる人間全員が「設備保全」ということを学ぶ必要があるのです。
- 設備保全とは?工場を安全に保ちつつ製造原価を1円でも安くする活動。
設備保全とは何か?
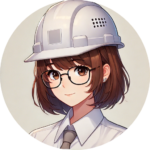
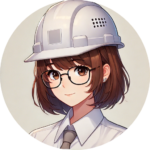
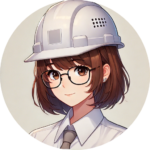
とりあえず工場を止めない活動が保全活動ですよね?
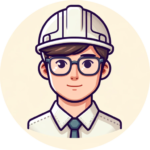
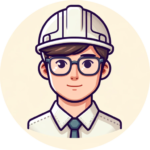
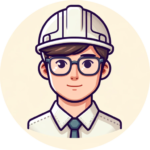
安全に保ちつつということも重要。あとは製造原価を1円でも安くすることも必要だよ
先ほども書きましたが設備保全というのは、「工場を安全に保ちつつ、製造原価を一円でも安くする行動」です。
なぜ安全が一番に出てくるのか?工場やプラント、特に価格プラントでは高温高圧の設備があり、それらを常に安全に封じ込めておく必要があります。
もしシールが壊れたり、回転機器が壊れて圧力が異常になった時に封じ込めるべき物質が漏れれば大事故につながります。過去にも多くの価格プラントで事後が起こり、時にば周辺住民にまで被害を及ぼしています。
そのような安全軽視の会社は社会から退場せねばなりません。そのようなことを防ぐためにも、設備保全をして事故を防ぐのは必須となります。
- 工場やプラントを安全に操業させるために設備保全が必要!
設備管理とは何か?
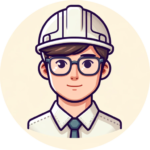
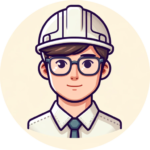
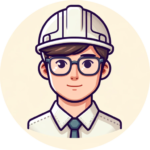
ちなみに設備管理とは何かわかる?
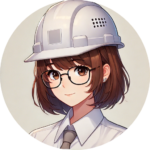
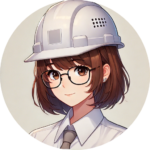
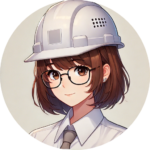
うーん、適切にメンテナンスをすることですかね?
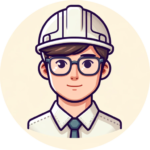
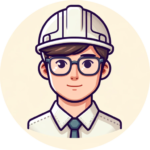
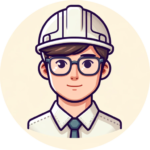
それも含まれているね!JISでなんと定義されているか見てみよう!
設備を管理するということはメンテナンスだけではありません。JIS Z 8141から引用すると
設備の計画、設計、製作、調達から運用、保全を得て廃却・再利用に至るまで、設備を効率的に活用するための管理
JIS Z 8141から引用
ということで設備保全も設備管理の中に含まれるわけですが、この保全の期間が一番長いのでいかに故障を排除して、正常で良好な設備の状態を維持するかが重要となります。
- 故障を無くす(低減ではなく0!)。
- 設備を正常で良好な状態に維持する。
- 生産設備を安全に稼働させる。
- 製品を常に安定して送り出す。
なぜ機械は壊れるのか?
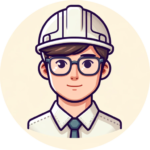
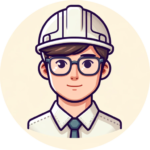
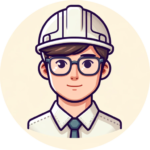
機械が壊れなければ保全なんて必要ない。じゃあなんで機械は壊れるの?
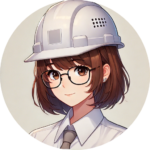
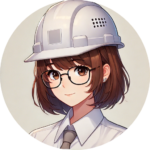
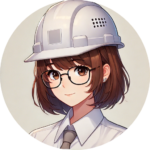
え?そんなの適切に使っても摩耗するし、時には腐食するからですよね?
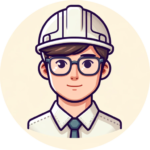
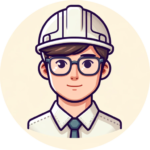
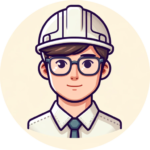
そうなんだ、つまり劣化しているんだよ!その劣化を把握して効果的に対処することが保全
設備保全が必要なのは機械が壊れるからです。機械が壊れなければいいのですが、そんな機械は世の中には存在しません。しかしここで単に「壊れたら直せばいい」という考えでは効率的な保全活動は進みません。
「機械は徐々に劣化してそれにより故障に至る」というふうに考えれば「劣化」を中心とした活動をすれば、自ずと故障を無くすことができます。
- 機械は徐々に故障して劣化する。劣化を中心とした活動が効果的
つまり保全活動というものは機械の劣化を正確に予測・把握して、その全てに対する網羅的な活動となります。
そのためには起こりうる全ての劣化に対しての計画的な保全活動が必要です。
- 全ての設備の全ての劣化を管理対象にしている。
- 故障物理、劣化のメカニズムを正確に把握して保全活動が行われている。
- 寿命を正確に把握する。
- 全ての劣化現象を確実に管理する。
劣化と故障の違い
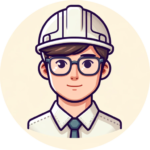
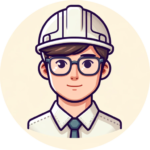
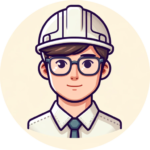
故障と劣化、この二つの違いは把握しておこう
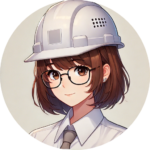
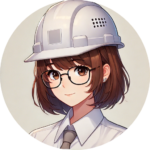
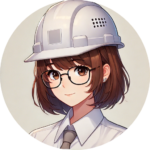
さっきの話しと似てますけど、つまり劣化するから故障する。であれば劣化に適切に対処すべきですね。
劣化と故障はどう違うのか?これを正確に把握していないと「故障したので交換する」という事後保全しかできない活動となります。
劣化とは故障に至る原因のことです。つまり機械が錆びたり徐々に摩耗したりする現象が劣化です。
故障はそれにより機能保全に陥ること、錆により配管に穴が空いて中の液体が漏洩したり、摩耗により軸にガタが出て所定の性能が発揮できなくなることです。
しかし、機能を失ったりすることだけが故障でしょうか?JIS Z 8141では以下のように定義されています。
規定の機能を失う。
規定の性能を満たせなくなる。
設備による産出物や作用が規定の品質レベルに達しなくなる。
JIS Z 8141より引用
つまり、品質トラブルなども故障と捉えることができます。
劣化と故障を正確に分類することは設備管理をする上で重要です。あくまでも劣化が進行して故障する前に何らかの手を施すのが、保全活動です。
- 劣化と故障は分けて考える!劣化を正確に把握して抑えることが重要!
故障率曲線とバスタブ曲線
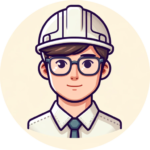
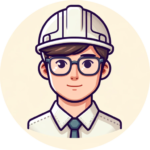
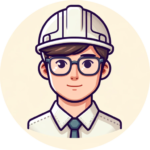
バスタブ曲線とは聞いたことはあるかな?
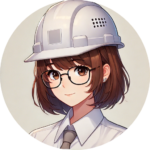
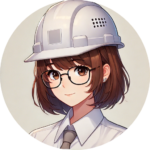
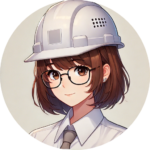
ありますよ!お風呂の風呂桶みたいになっているものですよね?
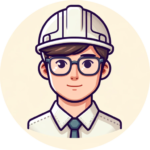
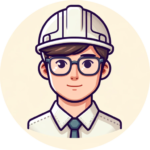
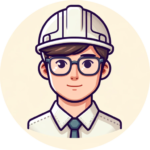
その通り!でも実際は1種類ではないんだ!
機械などの保全の話になったときに出るのがバスタブ曲線の話です。皆さんも聞いたことがありますよね?機械は入れたときは故障率が高く、安定すれば故障率が下がるが徐々に故障率が上がるという有名な曲線です。
このバスタブ曲線は故障の発生パターンとして非常に有名ですが、今では故障率曲線の中の一つとして扱われており、バスタブ曲線にピッタリと当てはまる機械はそれほど多くないと言われています。
ここでは「reliabilityweb.com」から画像を引用させて説明します。故障率曲線は以下のようになります。
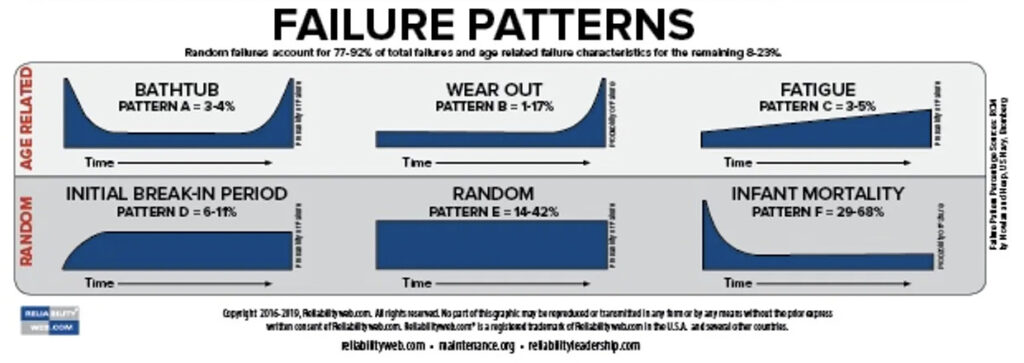
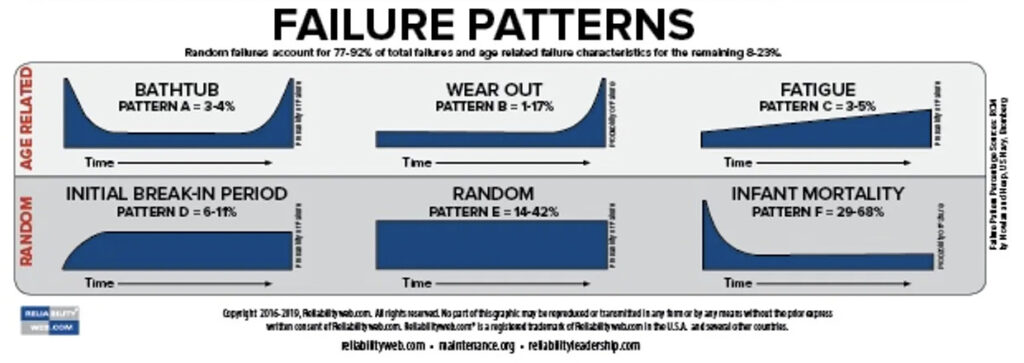
故障率曲線は大きく6個に分けることができ、さらに2グループに分けることができます。
上部3個は「AGE RELATED」つまり時間経過で徐々に摩耗していくタイプです。これらは「Time Based Maintenance(TBM)」つまり時間管理による保全活動が有効です。負荷が常に一定で摩耗や徐々に疲労していく部品などがこのパターンに当てはまります。
下の3個は「RANDOM」つまり劣化からの故障の発生が正確に予測できない部品となります。これらは負荷変動する部品などがこのパターンに当てはまります。これらは時間管理ができないので「Condition Based Maintenance(CBM)」が有効となります。
- 故障率曲線によってTBMとCBMを使い分ける!
もう少し細かく説明すると
- BATHTUB:一般的なバスタブ曲線。初期故障→偶発故障→摩耗故障の順に進む。
- WEAR OUT:初期故障がなく偶発故障→摩耗故障の順に進む。
- FATIGUE:摩耗故障域がない。疲労破壊する部品などが当てはまる。
- INITIAL BREAK-IN PERIOD:慣らし運転が必要な機械に多い。
- RANDOM:偶発故障のみ。突然壊れる可能性がある。
- INFANT MORTALITY:初期故障期間がすれば後は偶発故障のみ。
TBM?CBM?どっちを選ぶ?
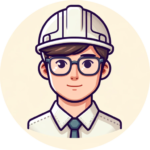
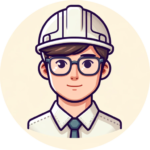
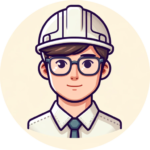
BM、TBM、CBMどれが最適かな?
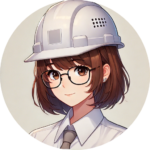
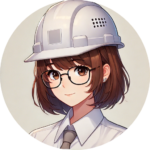
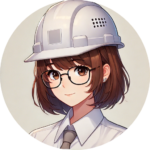
どれもその機械の故障形態から使い分けるべきですよね?
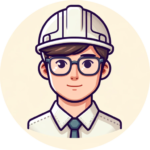
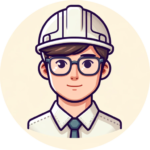
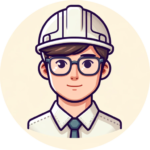
その通り!蛍光灯までTBMやCBMは必要ないからね!
設備の保全方式として有名なのが「BM」、「TBM」、「CBM」となります。細かい説明は省略しますがこのなかで「BM」は事後保全つまり壊れてから修理などをすることとなるので、これを減らす必要があります。
- (といってもそもそも事後保全対象、たとえば蛍光灯などは事後保全で問題ない。)
そして故障する前に何らかの対策を施すのが「TBM」と「CBM」になります。まず「TBM」と「CBM」の比較をします。
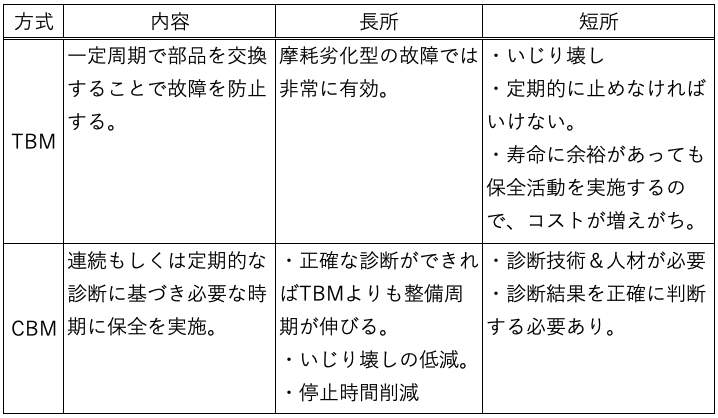
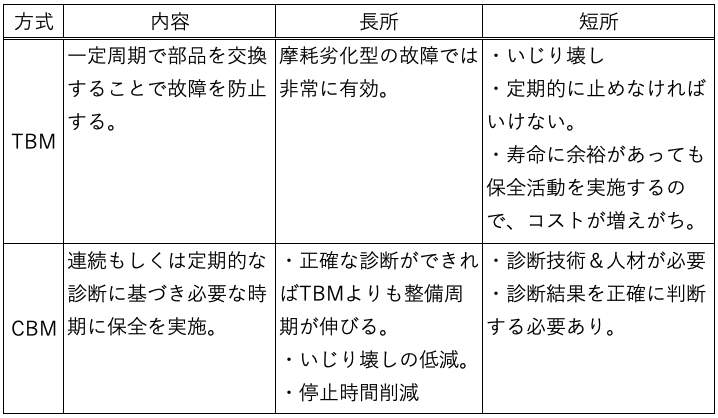
ということで全ての設備でTBMが当てはまったり、CBMが当てはまることもありません。部品単位で考えるとTBMとCBMが混在することになります。しかし、難易度としては「TBM」のほうがはるかに楽です。難しい設備診断もいらないですし、時間基準なので簡単です。
- 「TBM」、「CBM」それぞれ利点と欠点があるので使い分けることが必要!
それでもCBMを使うべき設備というのは下記のような設備になります。
- 非常に重要な設備
- 予備品が簡単に手に入らない。
- 停止すると損失が大きい。
- オーバーホールの費用が高額。
- 診断技術を適用可能。
- 一般的な監視項目では不足する。
- 故障した際に安全・製品に危険が生じる。
- 2次損失の可能性。
しかし、実際にはTBMと併用する場合も多いです。たとえば「◯時間経ったら交換。でもこの値が◯超えたら定修の時に交換」などですね。
ここまで説明した劣化を正確に把握して、その対象品に最適な保全方式を定め計画的に保全活動をしていくのが本来の設備保全となります。
設備保全の基礎知識まとめ
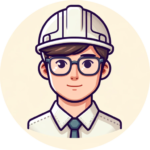
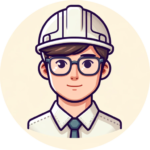
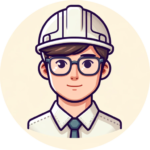
ざっくりと設備保全についてまとめたけどどうだった?
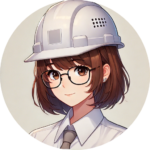
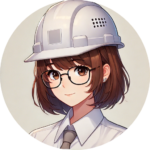
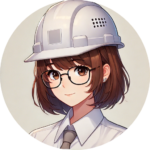
基礎知識からしっかりと学んでいかないと無駄にコストや時間を浪費しそうですね
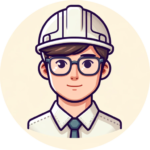
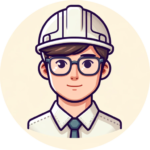
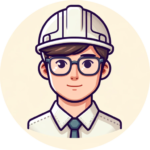
同じ機会でも部位によってTBMとCBMを使い分けるとか色々あるんだ。なのでしっかりと基礎知識を頭に放り込もうね。
設備保全は設備を導入してから最も長く続く活動です。しかし、プラントや工場、設備を安全に稼働させるには正確な知識のもとで設備保全を行うことが必要です。
故障に原因は全て劣化です。その劣化を把握してどのような保全体制で保全活動を実施していくかがとても重要になります。
コメント